Waste minimization
Basic approach
The Toyota Boshoku group verifies activities to reduce waste at each plant and deploys best practices across the organization such as reducing the defect rate and enhancing the recycling rate for components. We are also working on design and production preparations that realize a reduction in material loss rate.
Waste minimization
As part of Toyota Boshoku group efforts to minimize production waste, we are carrying out various initiatives to reduce emissions output rate by 14% by 2025, as compared to fiscal 2012 levels. To do this we are focusing both on minimizing waste during the production stage—such as by reducing the rate of defects, as well as by making improvements to yield—and on pushing forward with such activities as our upcycling initiatives. For example, the use of waste materials from car seat covers in the production of new products.
Additionally, as part of our efforts to reduce raw materials used in packaging during distribution, we are moving toward increased recycling of packaging materials. Similarly, we are reducing the use of packing materials by moving to reusable and “returnable” packaging, and by discontinuing excess packaging, such as so-called “double packaging” where multiple components of a product come individually wrapped.
Food waste initiatives: generating biogas from leftover food
Leftover food from cafeterias at Toyota Boshoku's Sanage, Fujioka, Toyohashi-Kita, Toyohashi-Minami, and Toyohashi-Higashi plants, as well as the Sanage dormitory, is used to produce biogas for charging forklift and tool batteries. Additionally, liquid reclaimed from the biogas production process is used as liquid fertilizer for the cultivation of vegetables. These vegetables have been offered as samples in cafeterias, and we are examining the possibility of using them as a regular part of our cafeteria menus in the future.
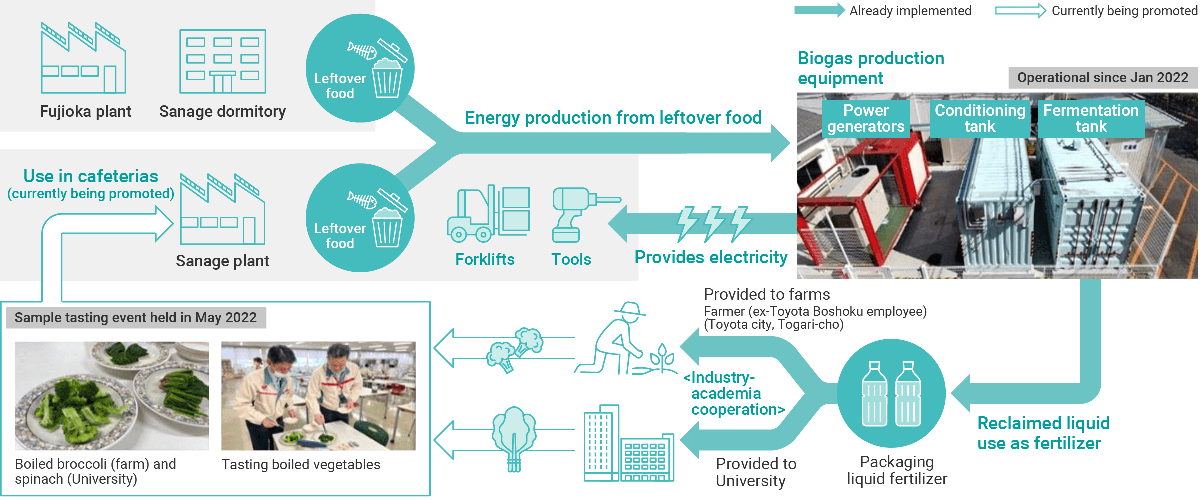
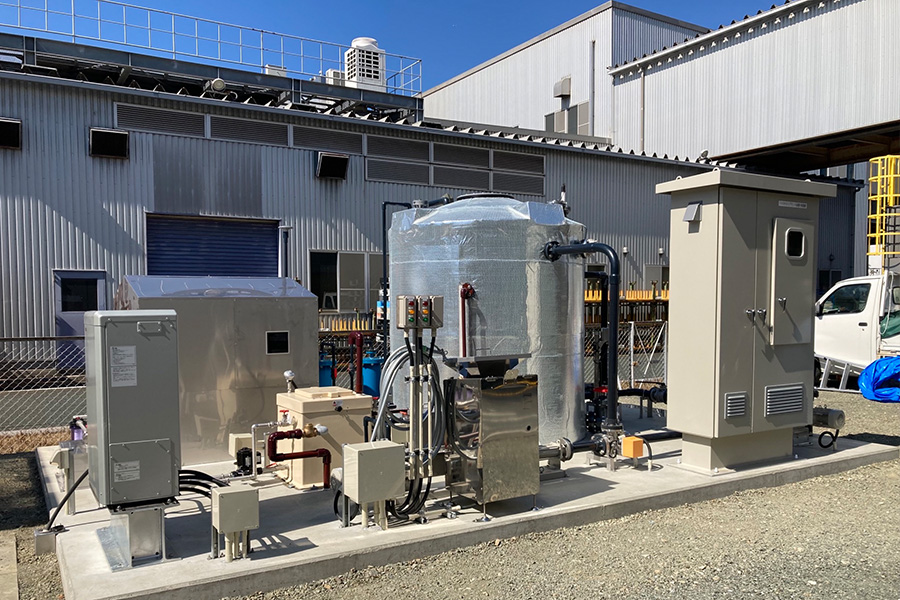
Initiatives to reduce waste by upcycling* surplus materials from seat covers
Toyota Boshoku-produced seat covers are made from comfortable, highly functional materials, offering a pleasant feel and texture, as well as flame-retardant and high-durability properties that prevent damage from abrasion, light, and the elements.
During production these materials are cut into shape, and some pieces are inevitably left over as waste. Similarly, when a line of seat covers is discontinued, some surplus stock may remain. In order to prevent waste and make full use of these high-quality materials, we have begun a project to upcycle them into new products.
As the first step of this project, we partnered with the Japanese baseball team the Chunichi Dragons to create a line of seat cushions based on their mascot Doala. We also produced chair covers for the Women's Japan Basketball League team the Toyota Boshoku Sunshine Rabbits.
In 2023, we trademarked the brand name RE:TERRACE for this upcycling project, and have expanded our offered products to include round cushions and slippers.
In the future, we will continue working towards carbon neutrality by making further use of waste and surplus materials from not just seat covers, but door trims, seat belts, and more.
- Upcycling: the act of taking something no longer in use, considering its potential, and reusing it for other purposes
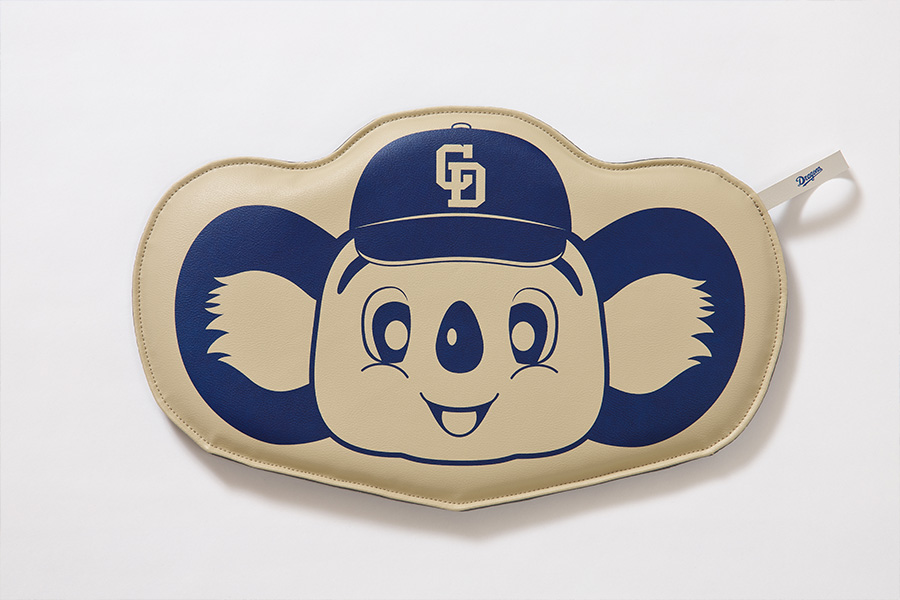

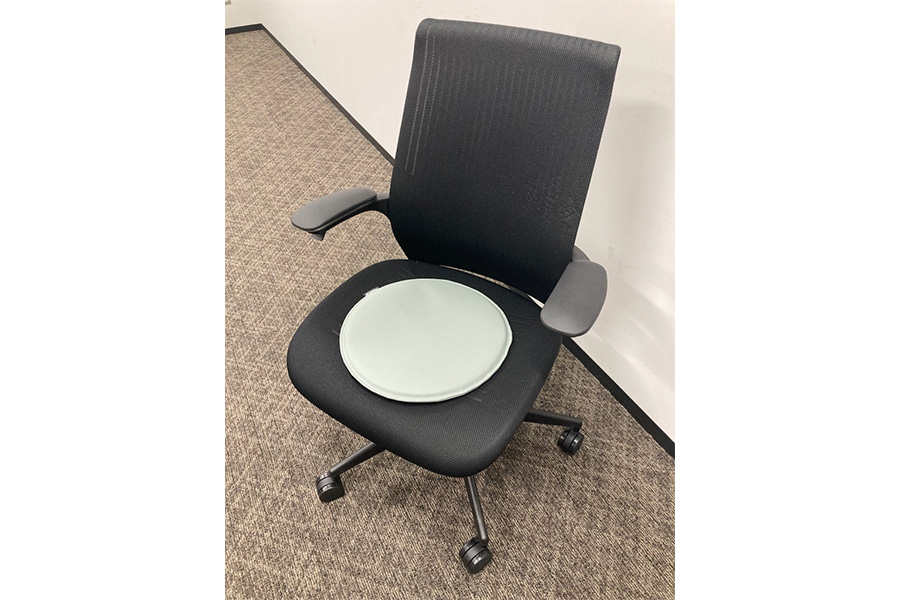
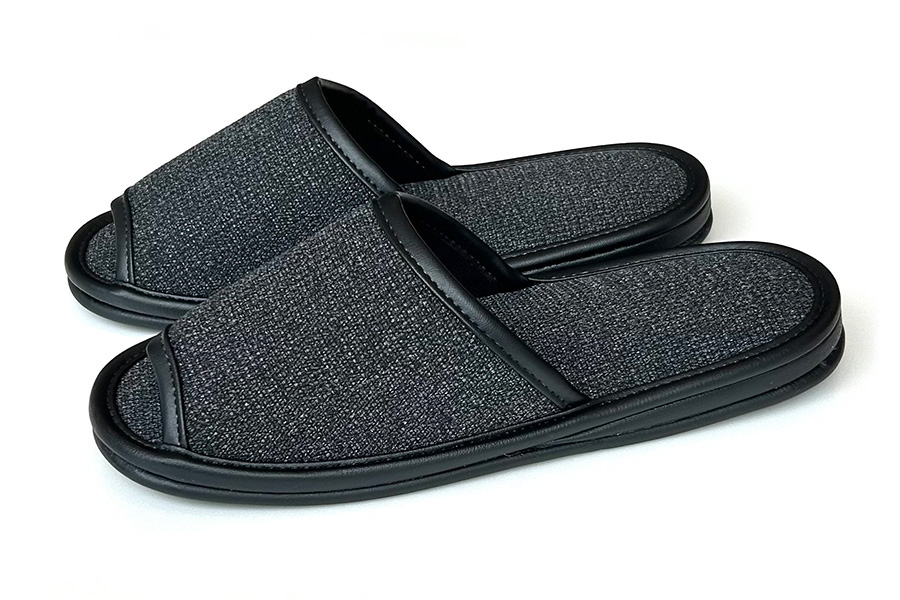
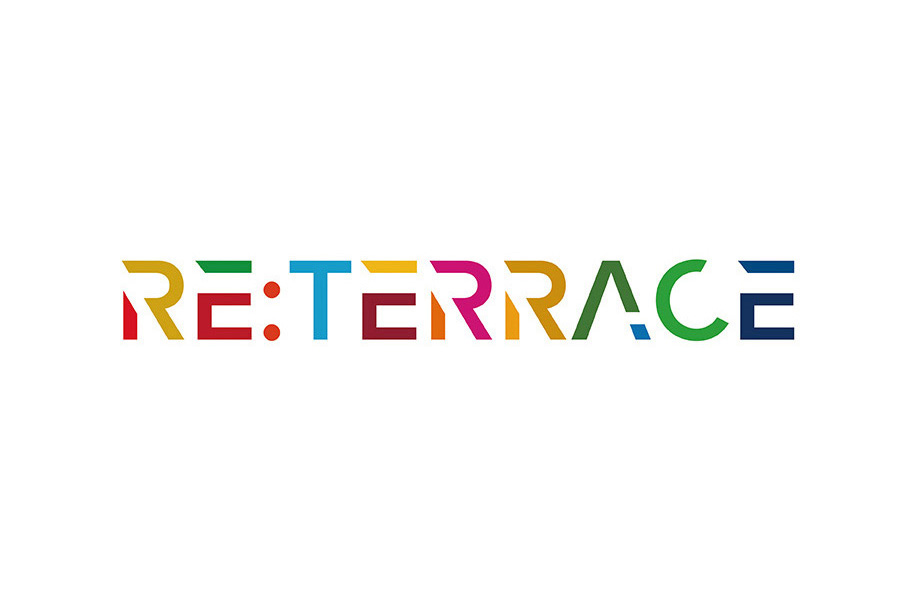