Expanded Kenaf Base Material
Contributing to carbon neutrality through the development of products using kenaf
Toyota Boshoku has been developing and producing internal components using kenaf—an annual grass—for many years.
Replacing conventional resin materials with foaming agents from kenaf boards has allowed reduction of mass, as well as reductions in CO2 emissions, which help us contribute to carbon neutrality.
For more information about kenaf, please see “Challenge of minimizing natural resources usage.”
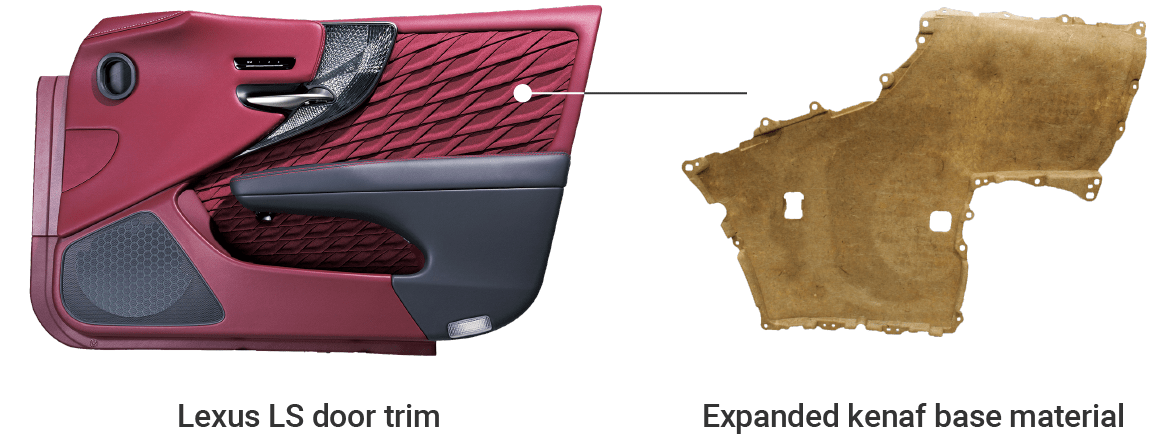
Main car models making use of expanded kenaf base material
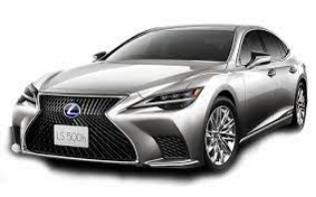
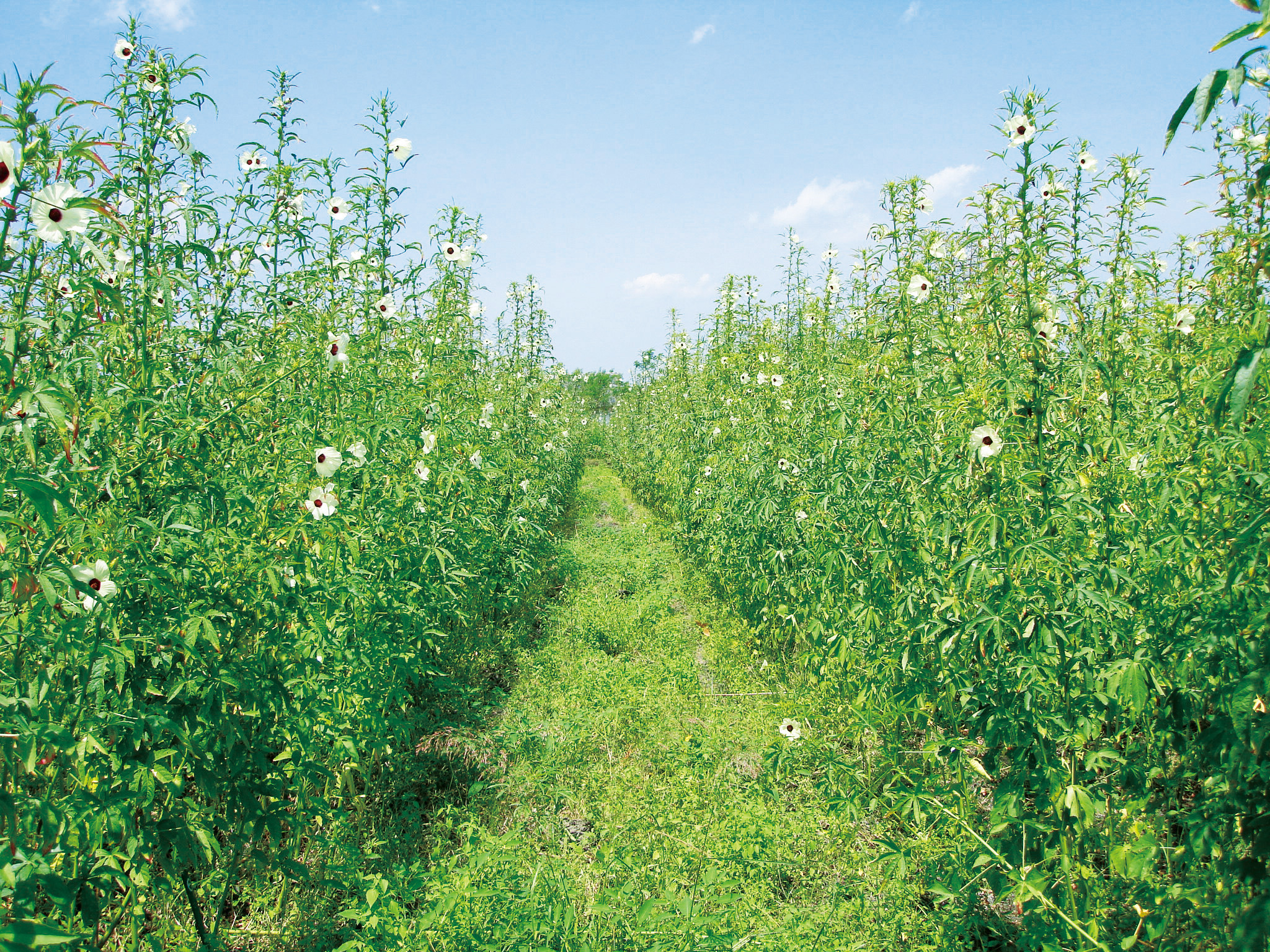
Toyota Boshoku’s Strengths
Since first using kenaf fibers in the base material for interior door trims in the year 2000, we have been building expertise and know-how regarding products that use kenaf raw materials.
Putting this know-how into practical use, we have developed expanded kenaf base material, and thanks to increased efficiency in production processes as a result of our Simultaneous Back-Injection Molding Technology, our efforts in bringing Competitive Kenaf products onto the market have been successful. We are now continuing to expand the range of car models that make use of kenaf products.
Click here for more information about Simultaneous Back-Injection Molding Technology.
Helping Change the World
Acting as an industry pioneer, Toyota Boshoku is promoting introduction and development of renewable raw materials to help curb the depletion of resources, such as through our continued use of CO2-absorbing plant-derived materials like kenaf in our products.
Additionally, we are working together as a group to curtail waste produced and water used throughout our production stages, and are proactively continuing with initiatives aimed at helping build a recycling-oriented society.