Human Resources Development
Basic stance
In order to develop people capable of contributing to society, who have diverse values, a challenging spirit and understand the value of strong teamwork, we have formulated the “TB Way competencies (the type of people we are looking for and job performance standards), based on our management philosophy, as our basic approach to developing and appointing human resources. We train and appoint people globally who can demonstrate well-balanced abilities in the four areas of “strategic planning,” “carries out the plan,” “strengthens talents and organization power,” and “humanity.”
TB Way, problem solving, on-the-job training (OJT), and policy management are the four Global Core Contents for sharing common values globally, and we are training and developing human resources on a global basis.
For human resources who will be the managers of the future, we provide global executive development program training, and training/placement as presidents of business entities outside Japan.
In addition, we conduct 360-degree evaluations and training assessments in the hiring process to carefully identify human resources, before making assignments and promotions. The human resource committee then holds discussions on succession plans for department managers, presidents of entities outside Japan, and top functional positions.
Global HR strategy
For the Toyota Boshoku group, an organization with many locations worldwide, a human resources (HR) strategy aimed at securing, assigning and fostering talents who can realize our growth strategy is a critical management challenge. We aim to recruit human resources with administrative and engineering skills, specialized skills and advanced expertise; assign them to appropriate positions; and make sure they are compatible with our growth strategy in accordance with our “global medium-term HR plan” that looks ahead to fiscal 2026. This policy supports the development of business.
Our Global HR Platform is a global common platform for management members and above. Through this platform, we realize the optimal global allocation of human resources and promote their development in order to maximize global organizational capabilities.
Application of Global HR Platform
Number of management positions globally
Fiscal year* | 2020 | 2021 | 2022 | 2023 | 2024 |
---|---|---|---|---|---|
No. of users under the Global HR Platform | 1,377 | 1,381 | 1,411 | 1,427 | 1,476 |
- Totals are stated as of April 1 of the following fiscal year
Proper manpower control, organization building, and human resources development
“We will nurture every individual in the Toyota Boshoku group, make maximum use of their competencies, and achieve the optimum results as an organization by having an appropriate organizational structure and span of control.” We have been developing the systems to achieve these goals. In particular, in the area of building an appropriate organization, we employed our management span of control guidelines and organizational templates, and have been aiming to continuously standardize the organization and strengthen human resource development since our organizational reviews in fiscal 2021, including affiliates from countries other than Japan and domestic affiliates.
’We are currently continuing to implement human resources development and allocation, systems for building an appropriate organizational structure, and manpower planning that we have developed to date, while focusing on the following two points, especially in regard to human resources development.
First, to establish a process for ensuring that the skills necessary for business execution are properly developed by enhancing and strengthening the links between the division of duties, important requirements for posts, skill maps, and development plans at an individual level.
Second, to ensure that the division general managers and direct supervisors think through the development plan and how it is implemented, assign challenging tasks, and develop talents together with senior company members in the workplace.
Through these efforts, we will continue to foster a culture of on-the-job training where each member can grow and maximize their competencies.
As well as this, we are carrying out cross-regional, systematic appointment/assignment of executive candidates based on discussions at the GSCT*1 and GSC*2. In addition, from fiscal 2025 we will start nurturing 100 talented company members who will lead the future of the Toyota Boshoku group (NEXT100*3), through global executive development programs (GEDP*4 and GLDP*5). Going forward, we plan to introduce a training program for outstanding personnel at the Senior Specialist grade, which will lead to the development of executives.
Through these measures, we are promoting the systematic development of management executives and are also fostering diversity (active appointment of non-Japanese, women, and young members.)
- Global Succession Committee by Top Executives: Executive management successor development committee comprising members at the Chief Officer level and above
- Global Succession Committee: Global key post (president of affiliate company, director, division general manager, etc.) successor development committee comprising members at the segment chief and field chief level and above
- Registration system for priority training individuals to strengthen the development of young people for the Toyota Boshoku group
- Global Executive Development Program: Selective training for mid-level executives
- Global Leader Development Program: Selective training for key talents and young executives
Specialized Skills related education
The Technical Skills Training Center supports improvement of workplace capabilities by providing knowledge-based education and practical training in order to develop members who can achieve a high level of safety, quality, delivery, and cost performance on a global level.
We have a system in place to ensure that all company members, including those with disabilities and those working reduced hours, have equal access to training.
We are also enhancing online training and strengthening global deployment.
Divisions and organizations targeted by technical skills training
Training system
FY2024 technical employee training attendance results
Name of training | Course content | Staff targeted by training | Total number of trainees | Average attendance time per person |
---|---|---|---|---|
Specialist technician training course(36 classes) | Sequence, hydraulic and pneumatic control, Karakuri, etc. | Skilled employees | 240 | 16H |
Basic skills training(12 classes) | Knowledge and skills to create quality products, and instructional methods to develop subordinates | Skilled employees | 42 | 16H |
Experiential manufacturing training for engineers(6 classes) | Seats, door trims, sewing, welding, etc. | Administrative and engineering | 132 | 16H |
Special training and qualification certification training(16 classes) | Industrial robot instruction, low-voltage electricity handling, high-elevation work, etc. | All employees | 939 | 8H |
Training for promoted members | Manufacturing supervisor, safety, quality, TPS, TPM | New plant managers | 138 | 32H |
New supervisors | 64 | 56H | ||
New team leaders | 151 | 64H | ||
General technicians | 247 | 24H |
FY2024 number of company members who passed the skills test
Expert level : 4 people
Level 1 : 27 people
Level 2 : 43 people
Outstanding Technician Awards
- Aichi Prefecture Outstanding Technician Award (Master Craftsperson of Aichi): 3 people
- Minister of Education, Culture, Sports, Science and Technology, The Award for Creativity: 5 people
Establishing Excellent MONOZUKURI Skills
Karakuri
Objectives
Karakuri refers to the manufacturing of a device employing simple mechanisms to solve problems and issues at the work site, created with wisdom and ingenuity while using as little artificial energy as possible. At Toyota Boshoku, we have implemented Karakuri training to instill a culture of Karakuri improvement, and are working to develop human resources.
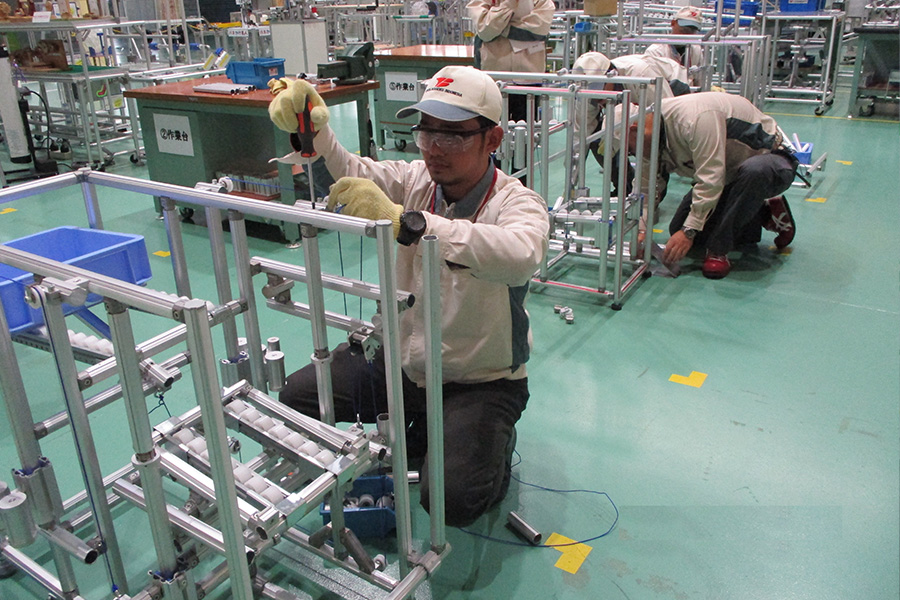
Checking the degree of development
<Karakuri Training Program>
Starting in 2020, we began accepting trainees on the one-year Karakuri Training Program, in order to promote improvements and advice, etc. using Karakuri at each workplace. In fiscal 2024, we newly established the Karakuri Kaizen Improver One Step Up Training Program, a one-month training program for affiliated companies in and outside Japan to improve the individual skills of company members, and are accepting group members to participate in the program.
(Participants in the Karakuri Kaizen Technician One Step Up Training Program in FY2024: 4 persons from affiliates inside Japan and 2 persons from outside Japan)
Affiliates inside Japan (Toyota Boshoku Tohoku/Toyota Boshoku Kyushu/Toyota Boshoku Shiga)
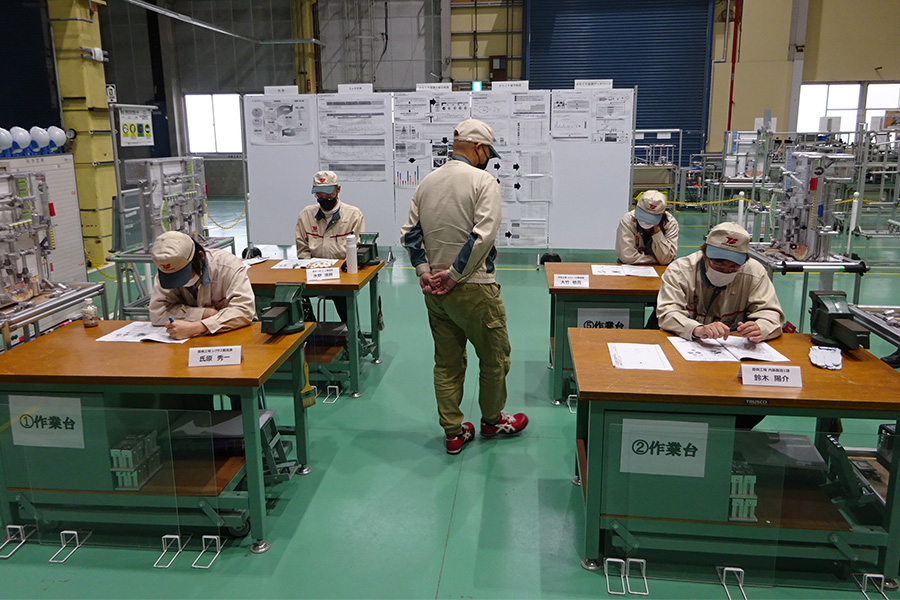
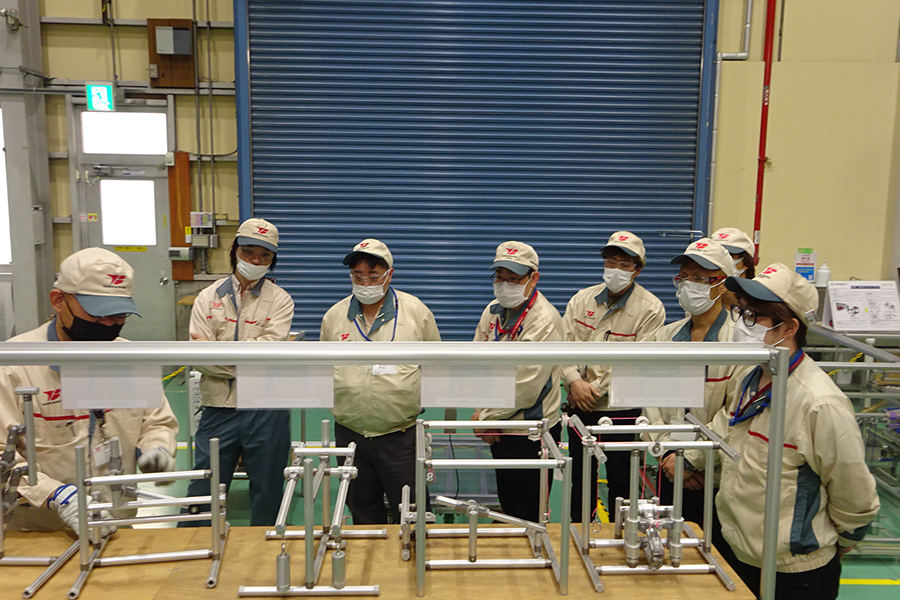
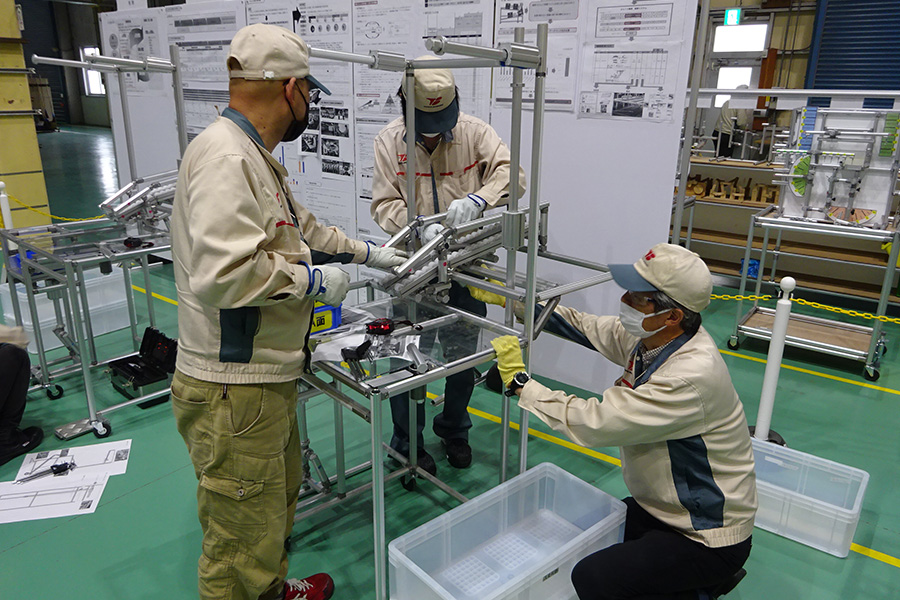
Affiliates outside Japan (Toyota Boshoku Indiana (US)/Toyota Boshoku Canada)
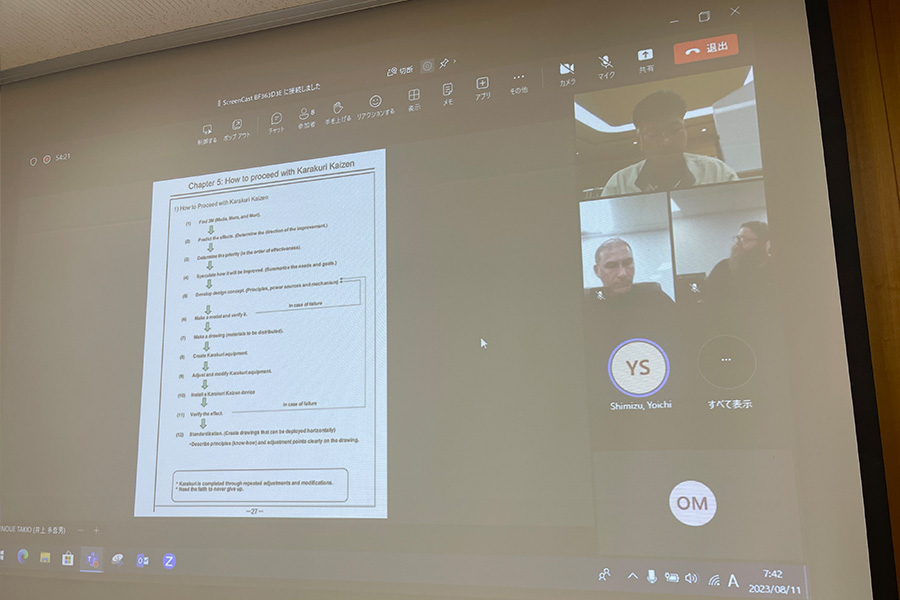
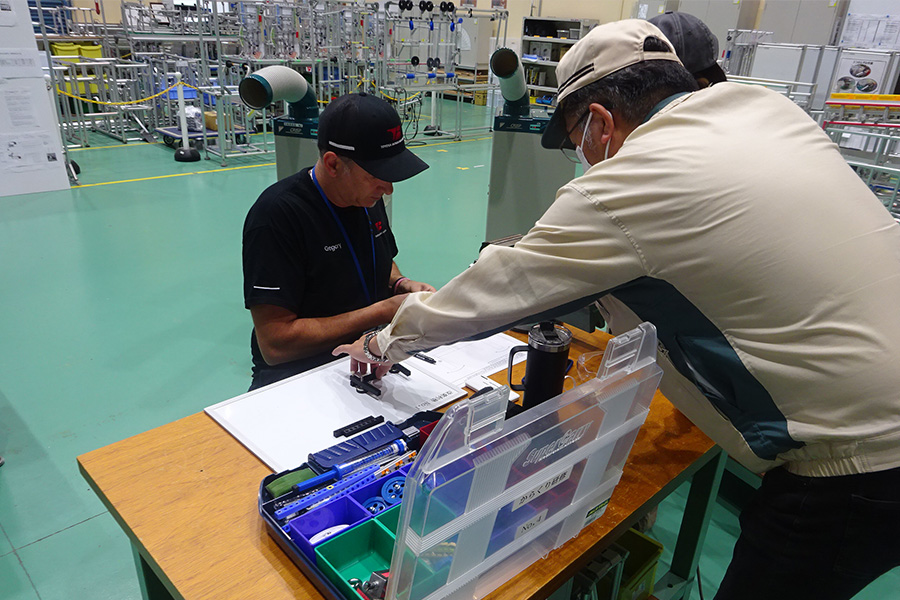
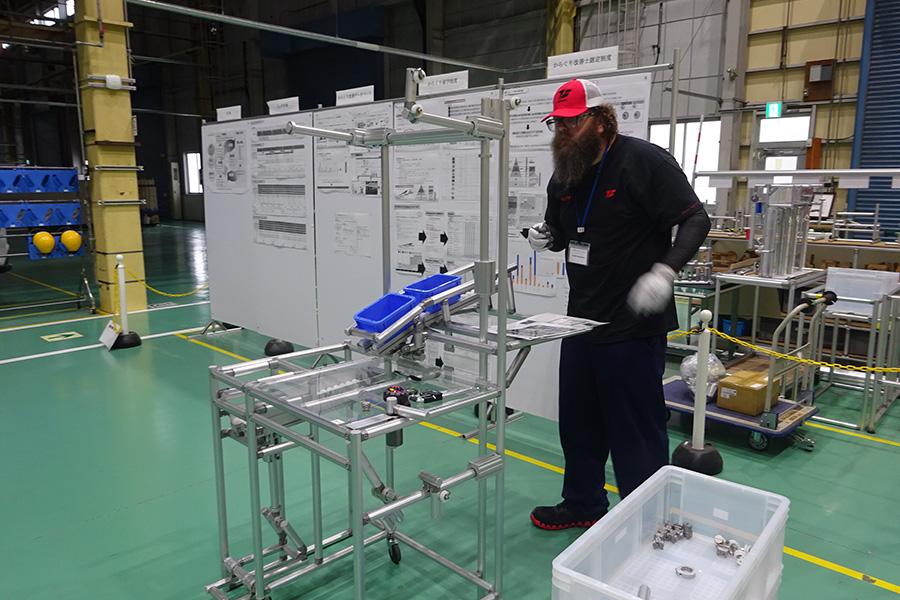
<Karakuri Kaizen Improver certification program>
The Karakuri Kaizen Technician certification program has been in operation since fiscal 2023 and has certified 173 people to date. By evaluating the ability to manufacture Karakuri devices and contribute to the workplace, this program leads to increased motivation at the work site and human resource development. It also reduces work hours at the site and contributes significantly to mitigating the site's environmental impact with a view to achieving carbon neutrality.
75 persons gained certification in fiscal 2024.
Number of persons certified as Karakuri Kaizen Improver [Toyota Boshoku Group]
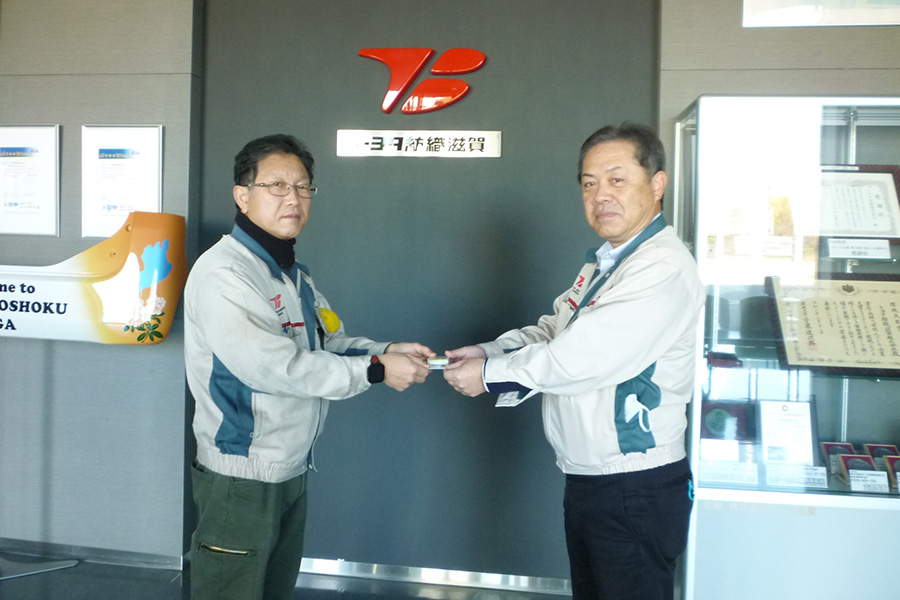
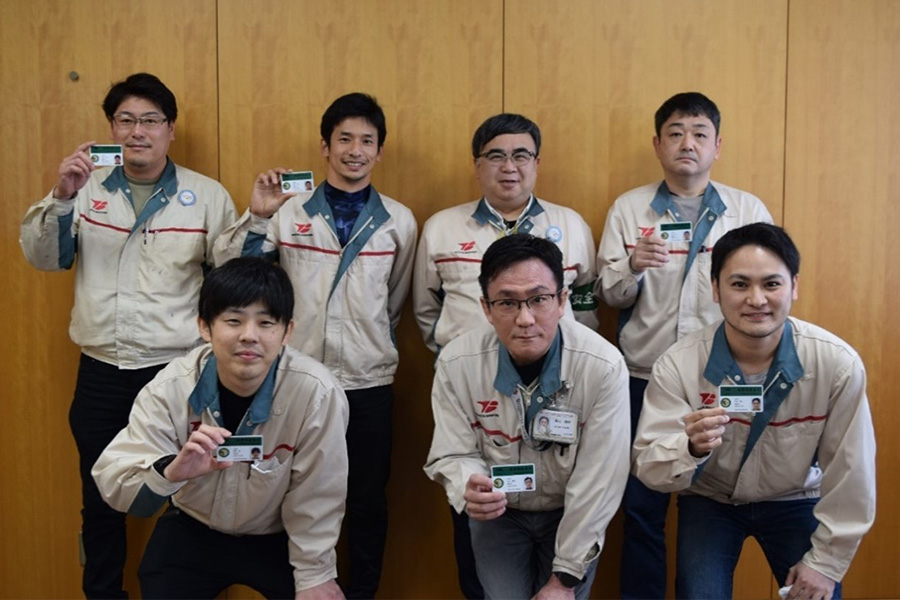
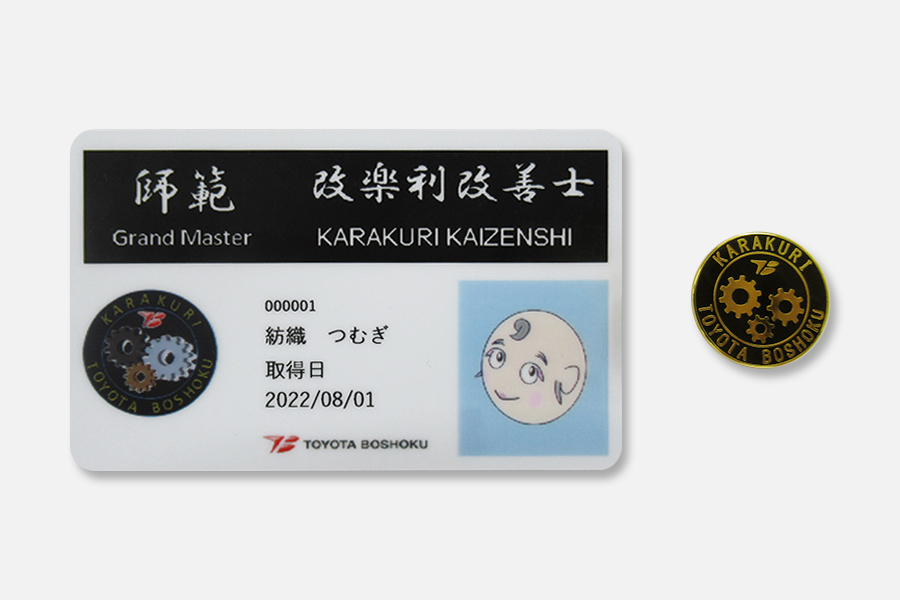
(Certification: Expert, Levels 1, 2, 3, and 4)
Work time reduction (improvement time) [Japan Region]
CO2reduction [Japan Region]
CO2reduction [Japan Region]
Results
Toyota Boshoku group exhibited eight examples of Karakuri improvement at the 28th National Karakuri Kaizen Kufu Exhibition in fiscal 2024. One of our exhibits was awarded a prize.
National Karakuri Kaizen Kufu Exhibition
FY | Prize |
---|---|
2014 | Prize for Excellence (2nd place nationwide) |
2015 | Association Special Technical Prize |
2016 | Grand Prize (1st place nationwide) |
2017 | Idea Prize |
2018 | Effort Prize |
2019 | Effort Prize |
2020 | Idea Prize |
2021 | Handcart Contest (Silver Prize) |
2022 | Constant and Fixed Quantity Extraction Contest (Gold Prize) Association Special Prize |
2023 | Idea Prize |
2024 | Idea Prize |
Won for 11 consecutive years and still winning!
Received the Idea Prize in FY2024 for "Rakuraku-kun," which relieves heavy manual work
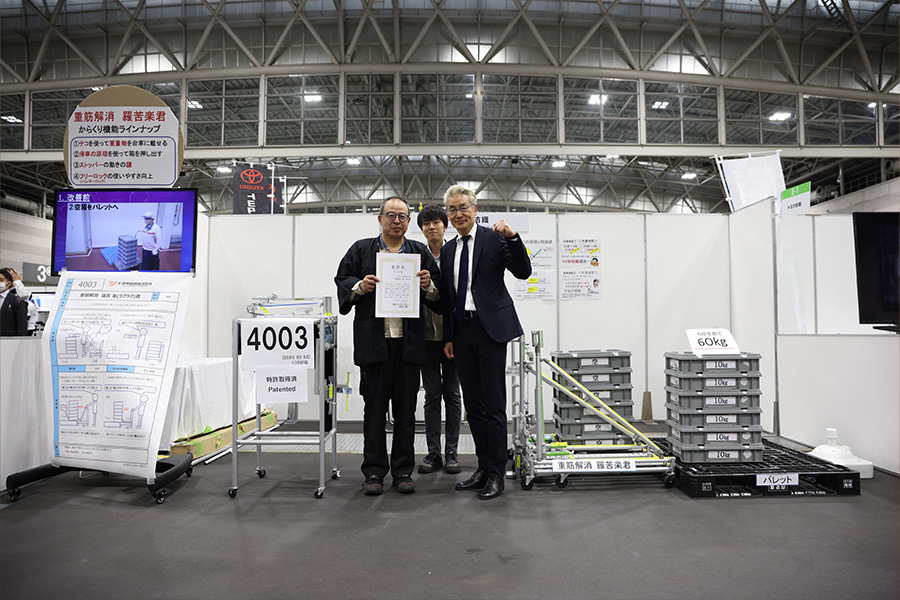
All Toyota Boshoku Skills Competition
The All Toyota Boshoku Skills Competition was held to verify the degree of development of technicians.
Fiscal 2024 was the first time in four years that the event was held globally. A total of 205 entrants from Toyota Boshoku, its subsidiaries and affiliates inside Japan, as well as from other locations outside Japan, took part in a spirit of friendly rivalry. Like last year, all categories were live-streamed so that those who were unable to attend in person could watch the heated competition.
In the Karakuri category, an affiliate from outside Japan taking part for the first time won a top prize.
Skills Competition opening ceremony
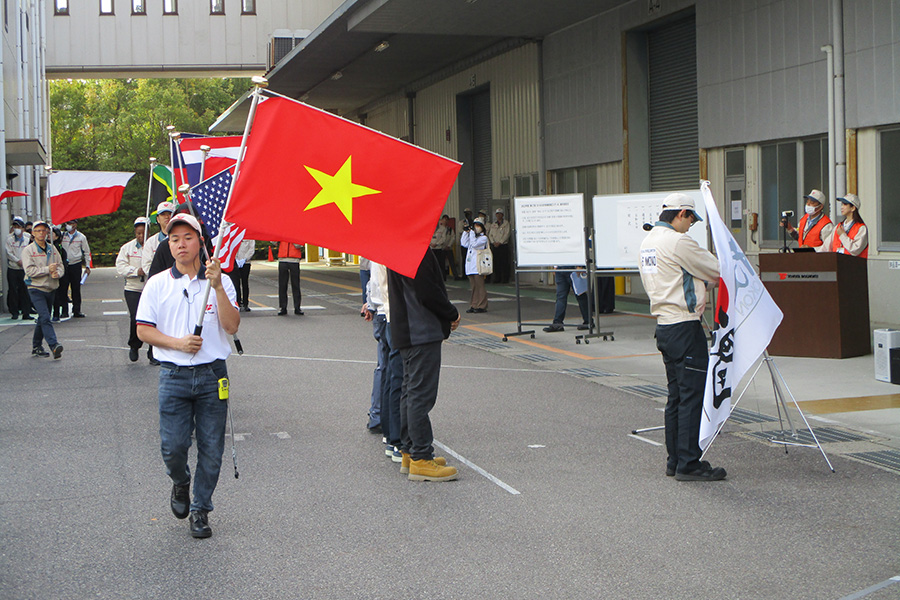
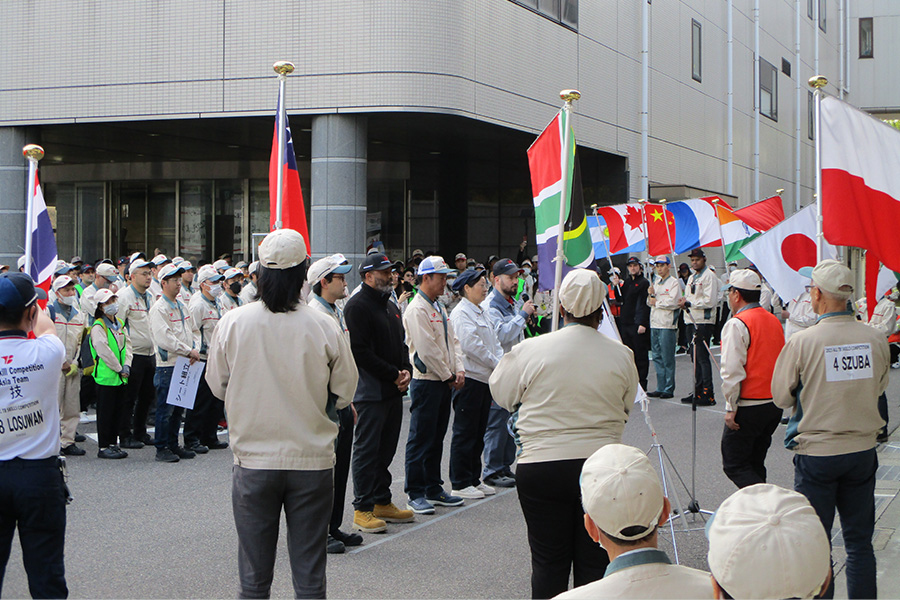
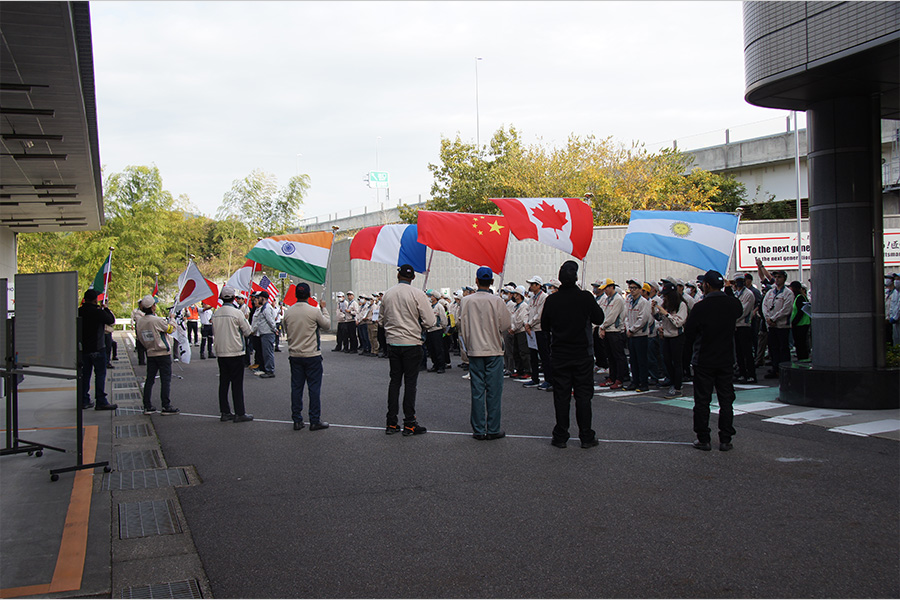
Skills Competition events
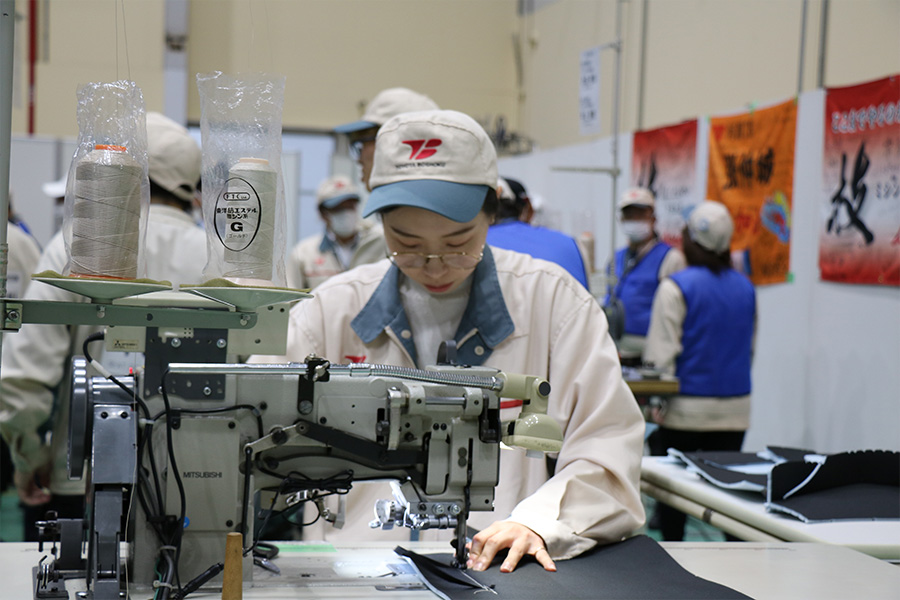
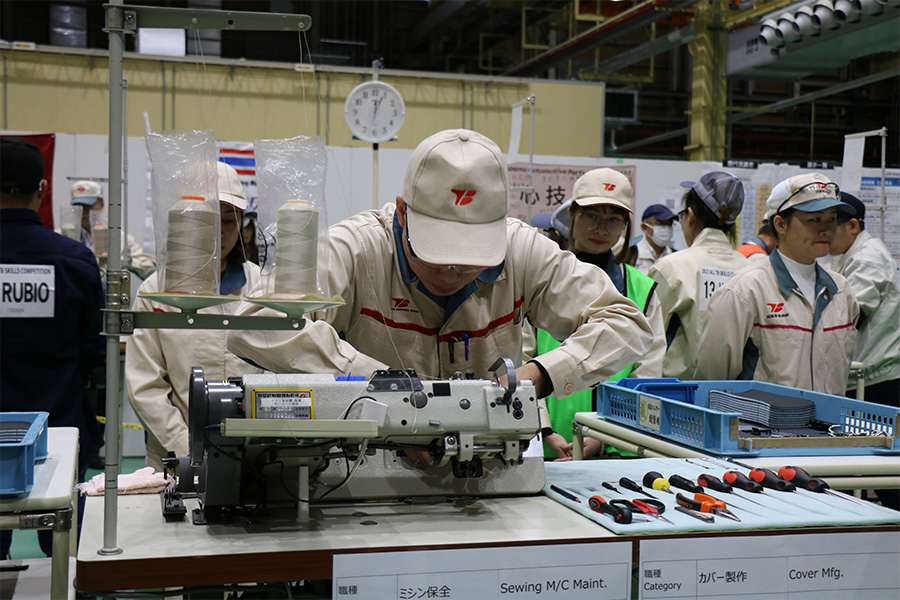
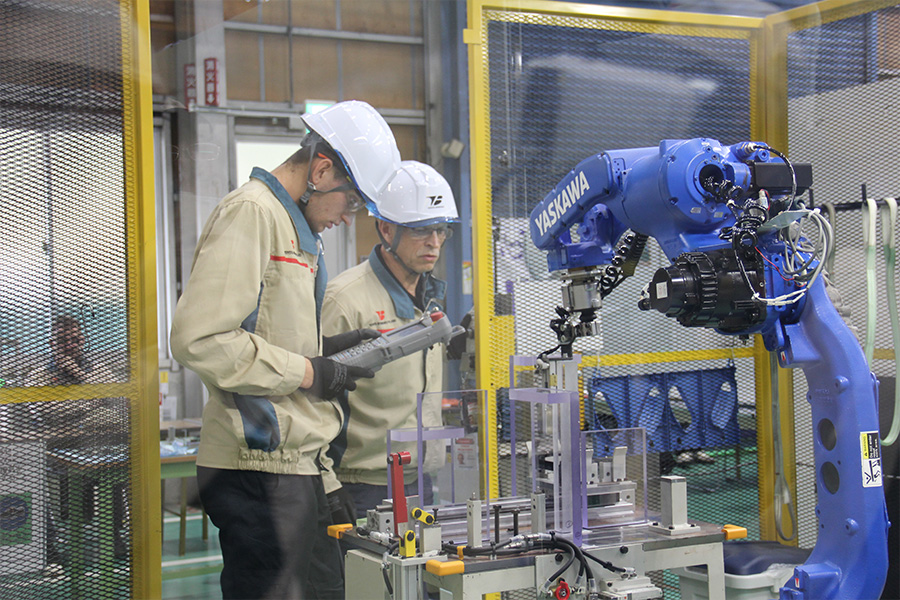
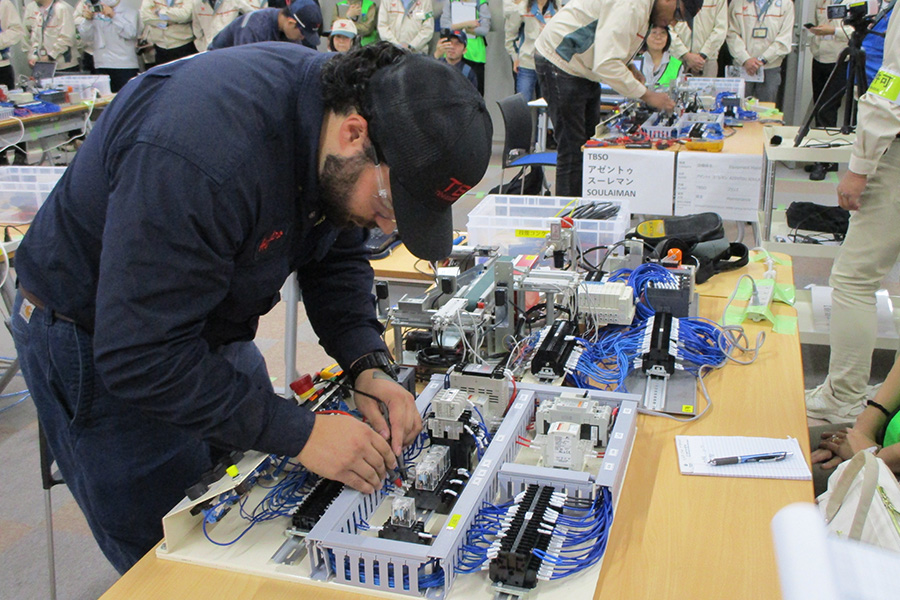
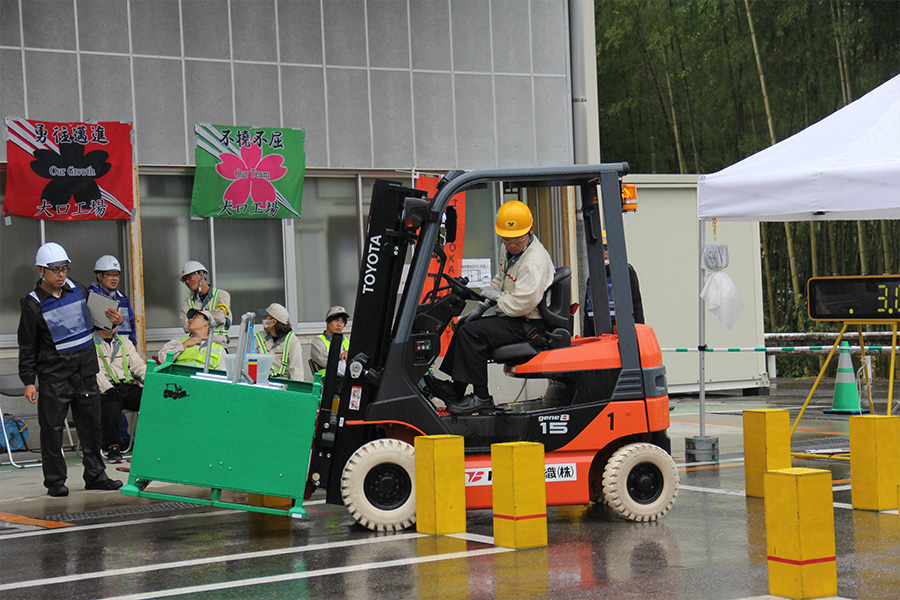
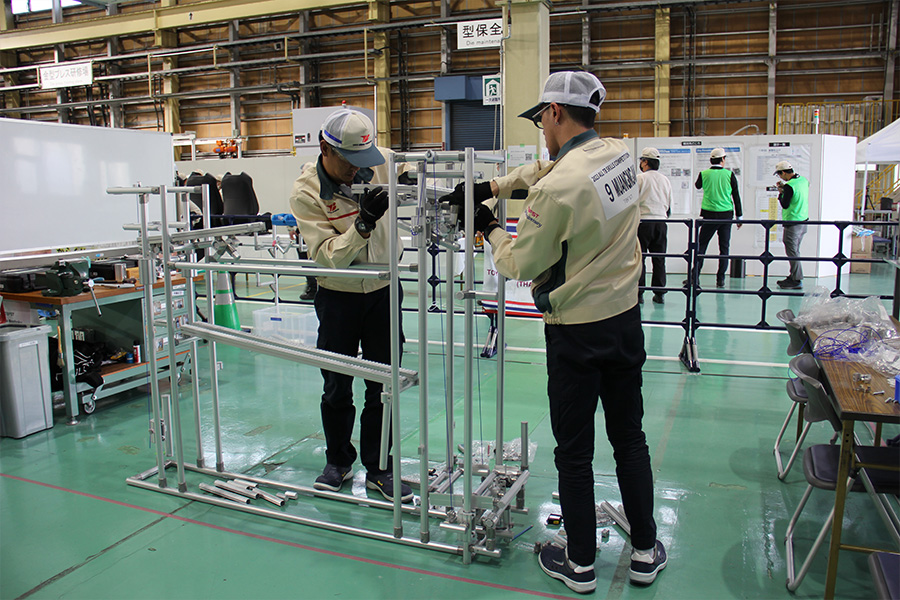
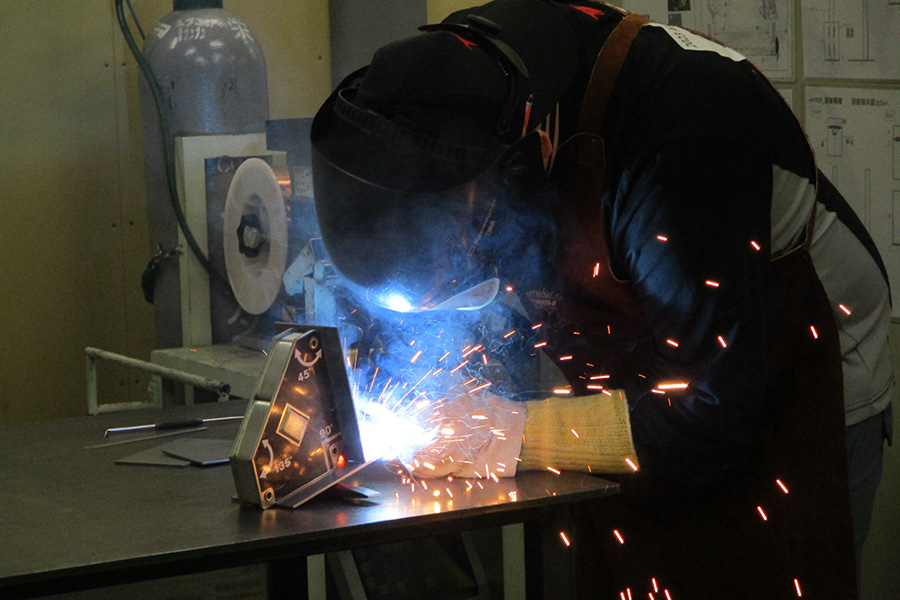
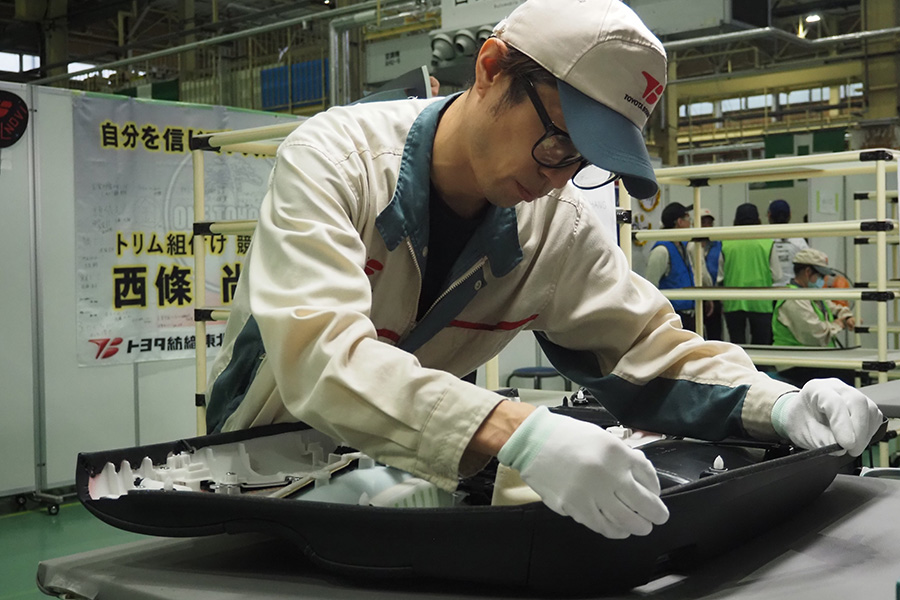
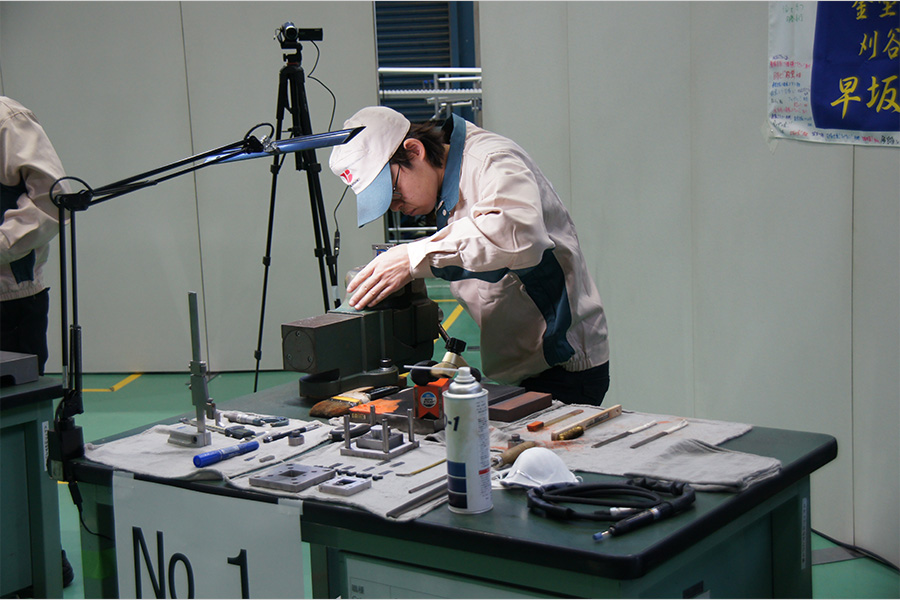
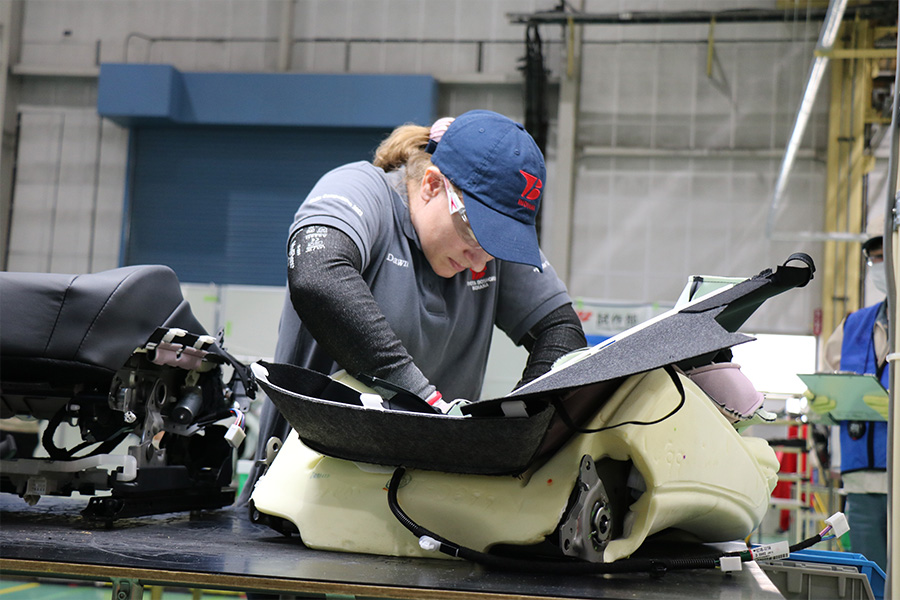
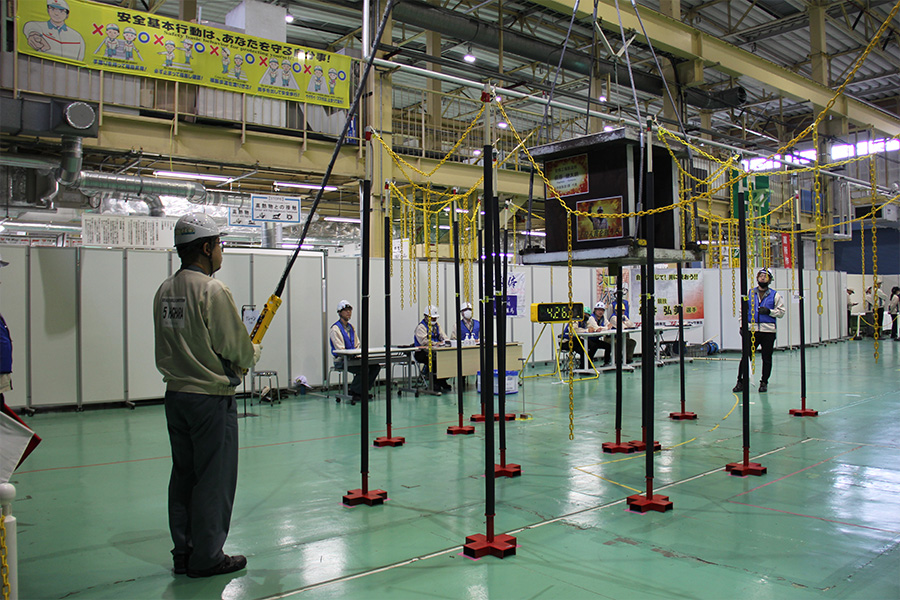
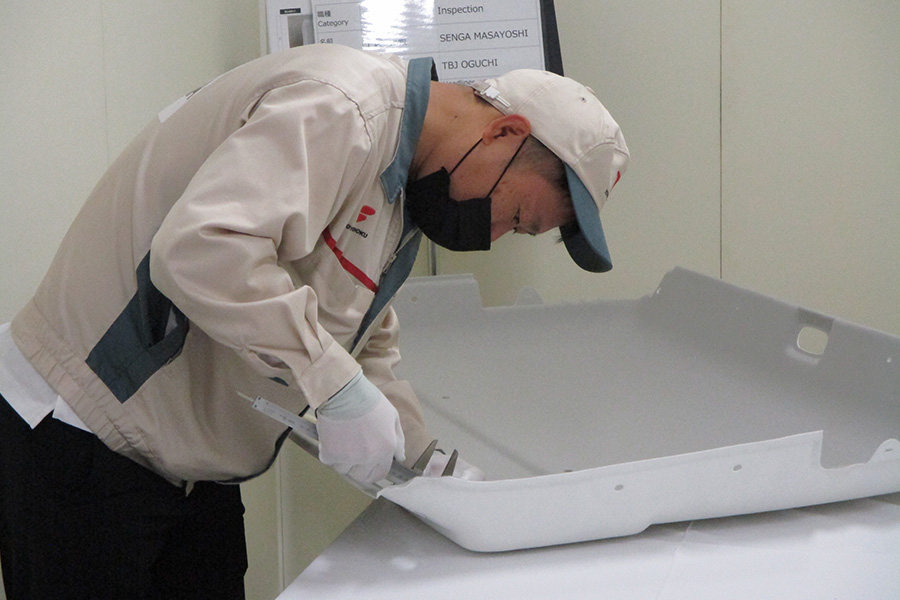
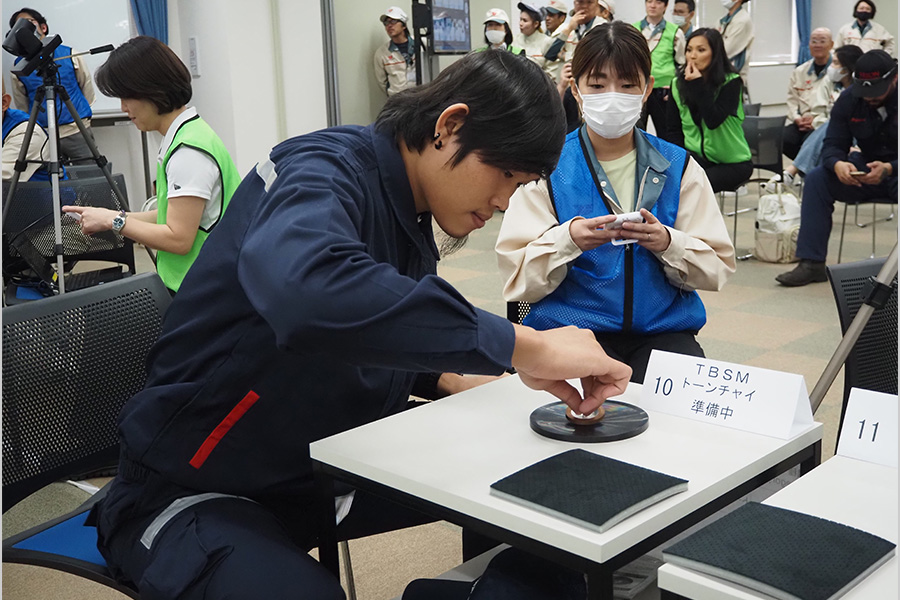
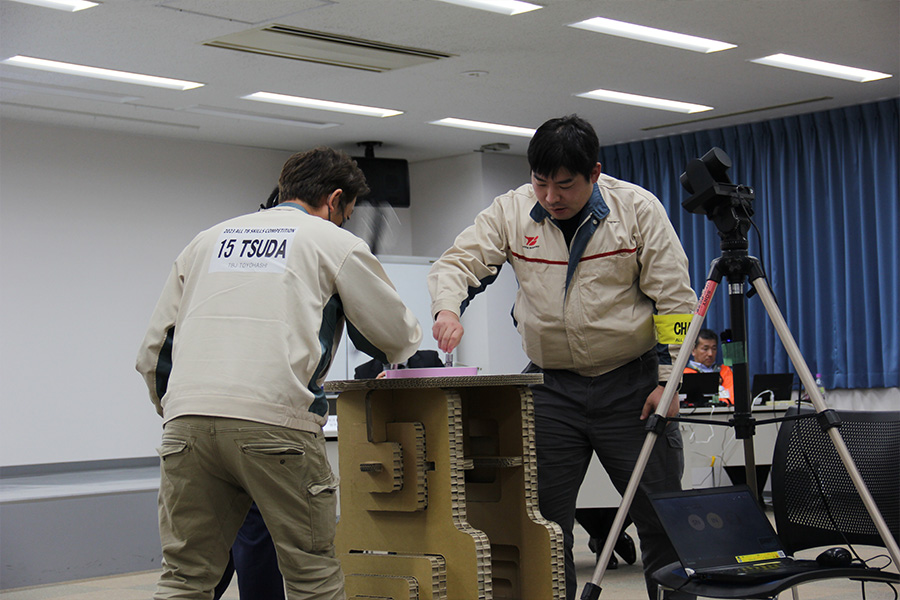
- a competition in which the participants make use of their creativity and ingenuity to design and fabricate their own “koma” spinning tops
Developing strong managers and supervisors
To develop technicians and supervisors who can work at the forefront of our manufacturing sites, we provide training by job level and skills training. As a first step in promoting training globally, the Manufacturing Skills Development Division, newly established at Toyota Boshoku America (TBA), and Toyota Boshoku Indiana (TBIN), a manufacturing site, collaborated in fiscal 2024 to begin developing a training environment for technicians.
First, based on the three concepts of "repeatable training," "quantitative evaluation," and "one-person training," a seat assembly training jig was developed and a visual manual in video format was introduced to facilitate understanding of so-called "kankotsu" areas (involving intuition and skills). This has now evolved into a dojo used when taking on new company members and for multi-skills training.
Next, we began to develop a training system to enable the training of strong supervisors, and started training for team leaders (Team Leader grade), which had been the biggest issue at the site.
In fiscal 2025, we will complete establishment of the TBIN development program and expand it to the Americas region.
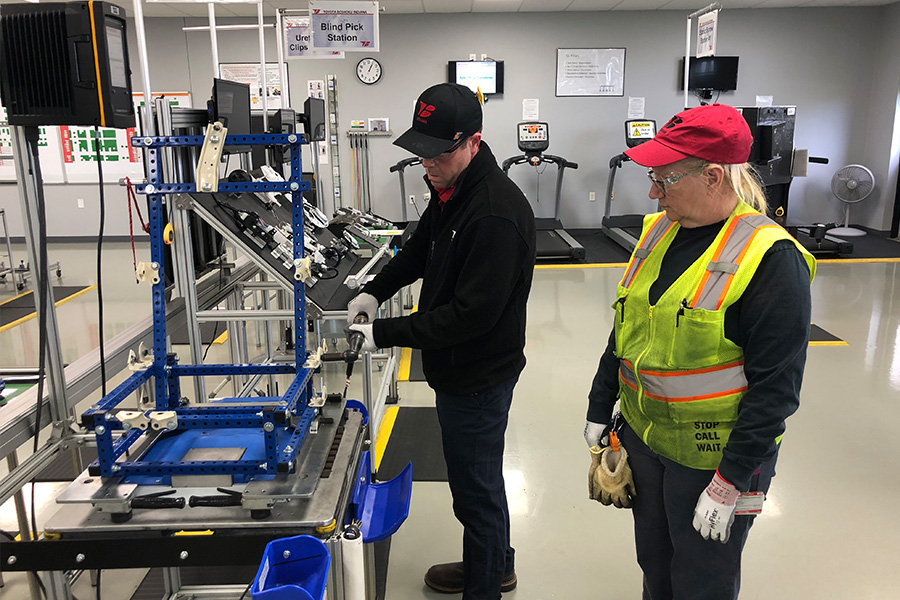
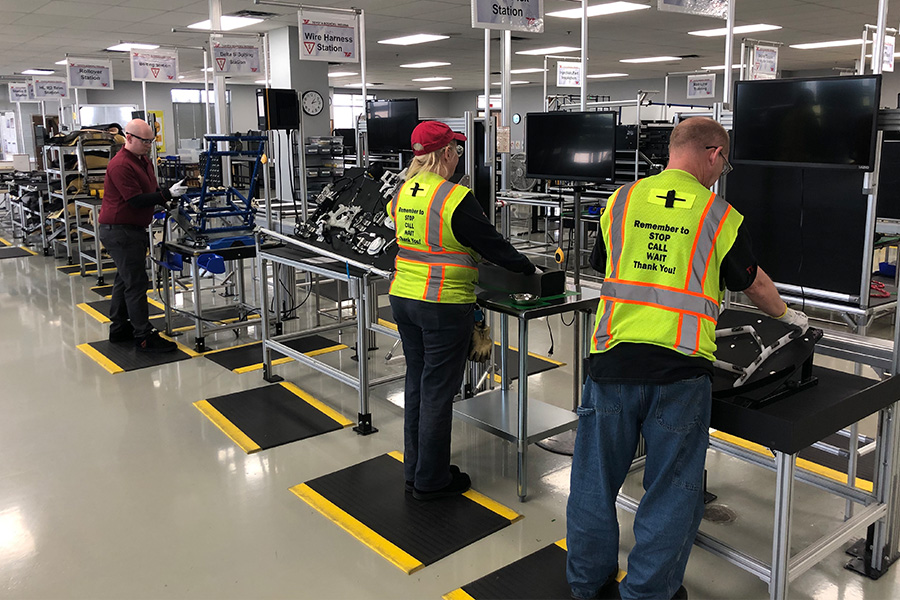
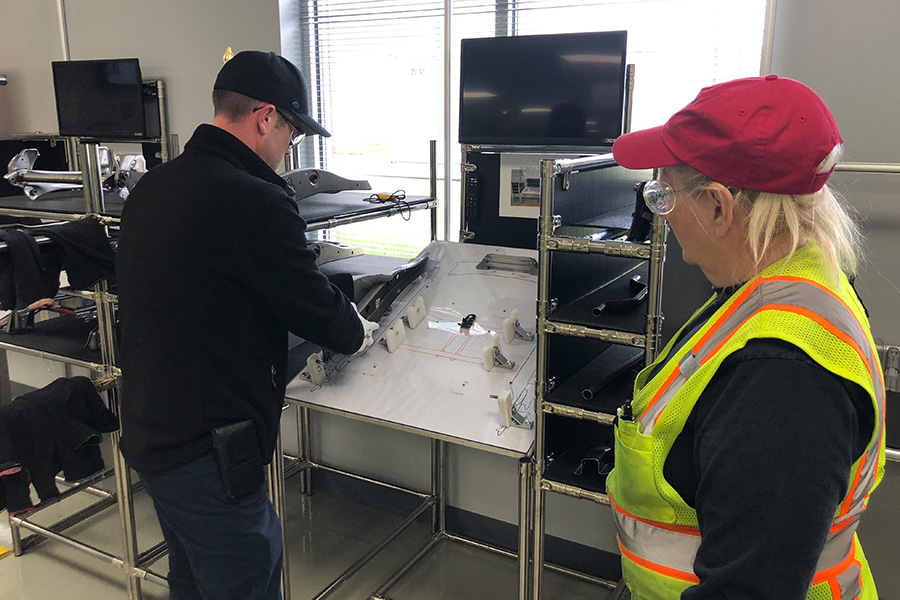
Strengthening Maintenance Skills
We are working to improve maintenance skills by establishing new courses for technicians involved in assembly and maintenance work for equipment and molds, in line with changes in the way work is performed in the field.
TBA's Technical Skills Training Center, which opened in fiscal 2019, has set up new courses and is training new instructors. In the future, there will be a need to develop skilled personnel who will become the core of the maintenance division and who can respond to an ever more changing manufacturing environment. We will develop new training in cooperation with the Production Engineering Division in order to develop technicians with the skills to handle new technologies and systems such as collaborative robots and image processing.
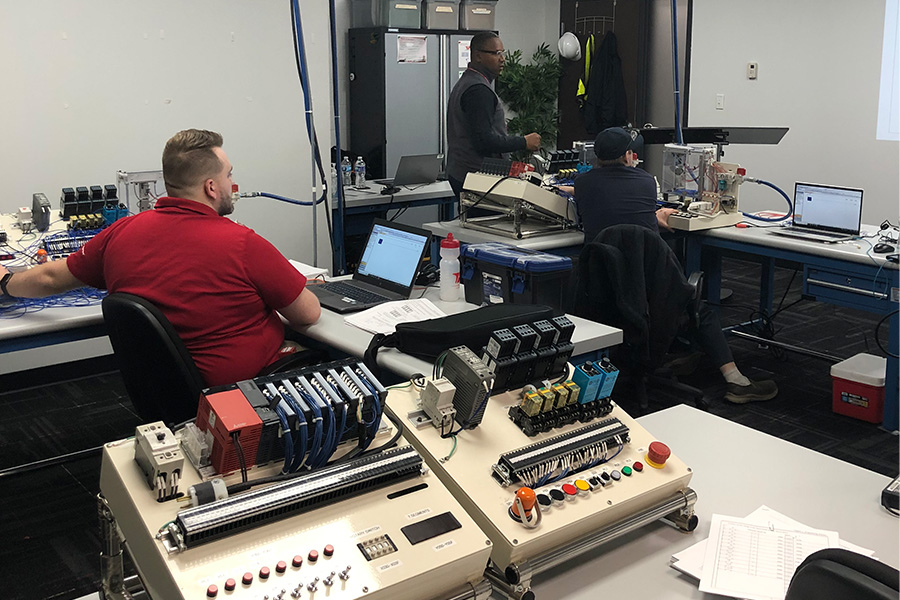
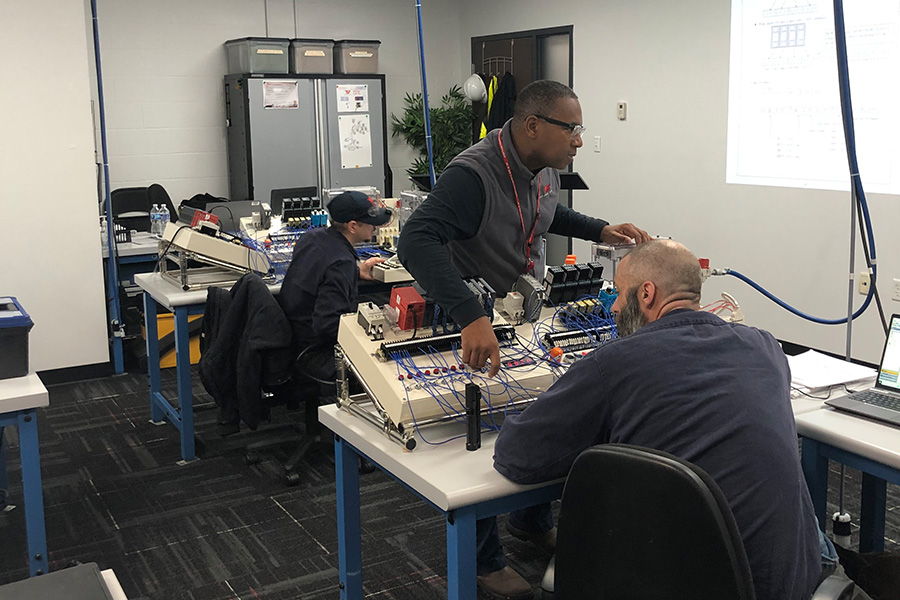
Toyota Boshoku Technical Skills Academy
We are promoting the development of a core of young skilled human resources who can work globally with a good balance of mind, body, skills and knowledge. Every year, we nurture company members who can thrive in the workplace through various experiences such as training in Canada and exchange programs with other academies. As well as within Japan, younger company members from regional entities outside Japan are learning, and in this way, we are developing human resources for the whole of Toyota Boshoku.
Consecutive wins at the National Skills Competition, including gold prize
We are participating in skills competitions with the aim of developing human resources who can serve as the future leaders of technical workplaces at Toyota Boshoku.
In November 2023, 12 members of the Toyota Boshoku Technical Skills Academy competed in 4 categories at the 61st National Skills Competition held at Sky Expo in Aichi Prefecture, winning gold prize in the Mechanical Engineering Design-CAD category. In addition, two members of the Mechatronics category A Team won silver prizes, and a silver prize was also won in the Plastic Molding category. Mechanical Engineering Design-CAD will represent Japan at the 47th WorldSkills Competition to be held in September 2024, aiming for the global top spot.

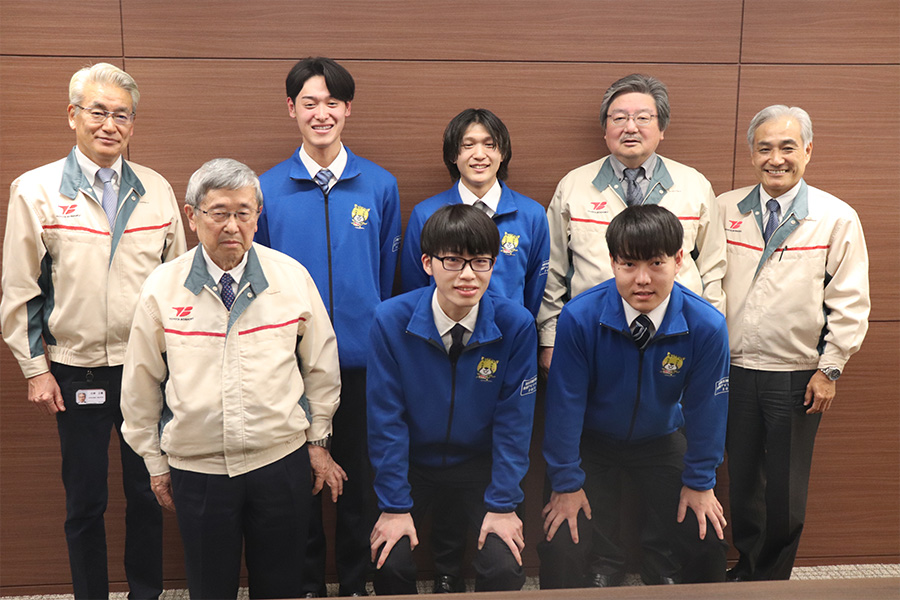
Graduates association “Kibo-no-kai”
In 2014, five years after the establishment of the Toyota Boshoku Technical Skills Academy, we established the graduate association “Kibo-no-kai” to help graduates develop ties with both older and younger graduates of the Academy as well as ties with classmates from the same generation, and for their mutual support. This has made it easier for the leaders of each workplace to collaborate and to make even greater contributions to the company. We also provide support for a wide variety of activities, including the self-development of members and the Academy’s club activities.