Sustainable resource circulation
Basic approach
The Toyota Boshoku group will contribute to curbing the depletion of fossil fuel and mineral resources by promoting easy-to-dismantle and recyclable designs, recycling materials through the development of recycling technologies, and replacing materials through the use of plant-derived materials.
Automobile interior components using kenaf
Aiming to reduce GHG emissions in the life cycle of automobiles, we are promoting the development of products using kenaf, which are widely used in automobile parts.
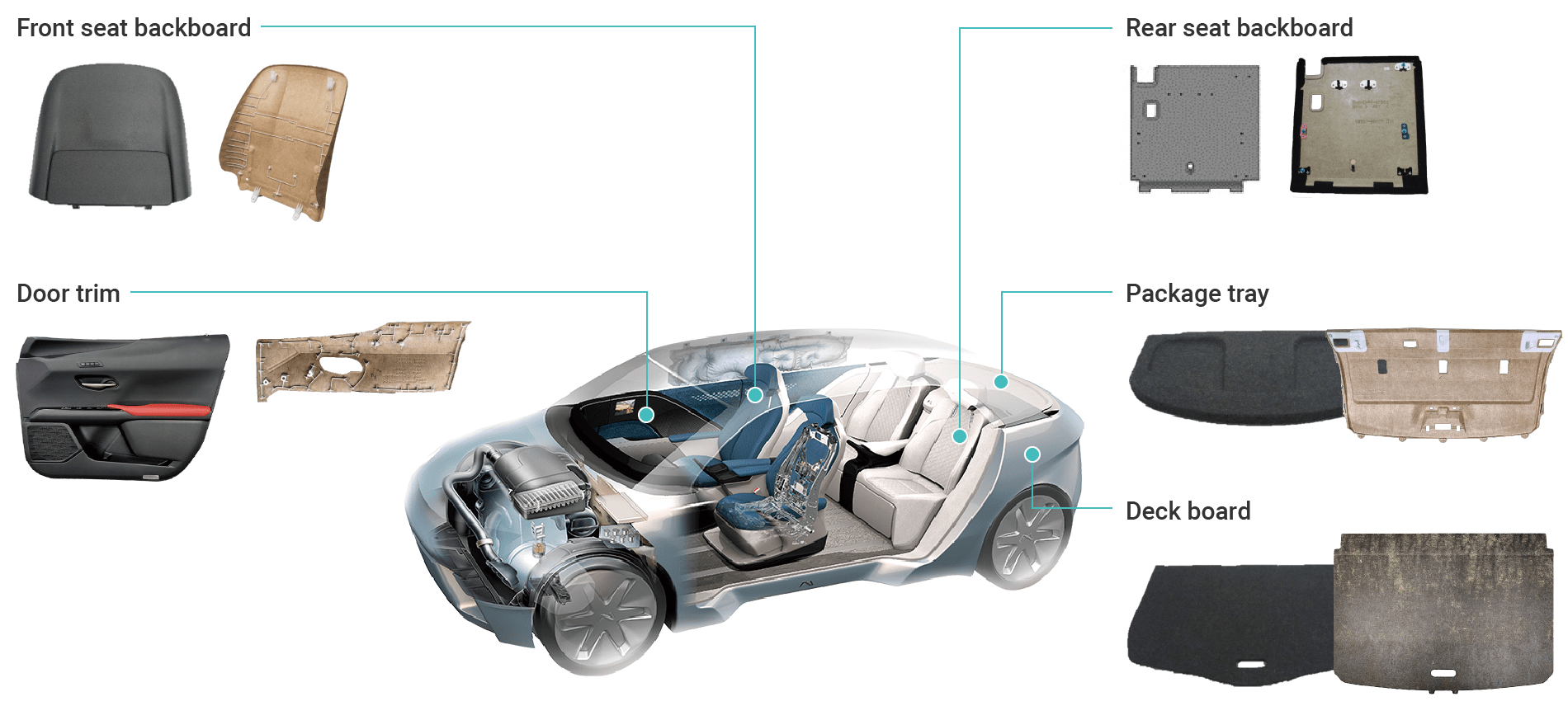
Life cycle GHG reduction benefits (from raw material production to disposal)
By replacing petroleum-based materials with plant-based materials for interior components and using kenaf, with its strong fiber, as a reinforcement material, it is possible to improve fuel efficiency (reduce CO2 emissions during driving) through lightweighting.
What is kenaf ?
CO2 absorption capacity
It grows rapidly, reaching a height of 3 to 4 m and a stem diameter of 3 to 4 cm in about six months. It is an annual plant that also has a high CO2 absorption capacity.
How kenaf products are made
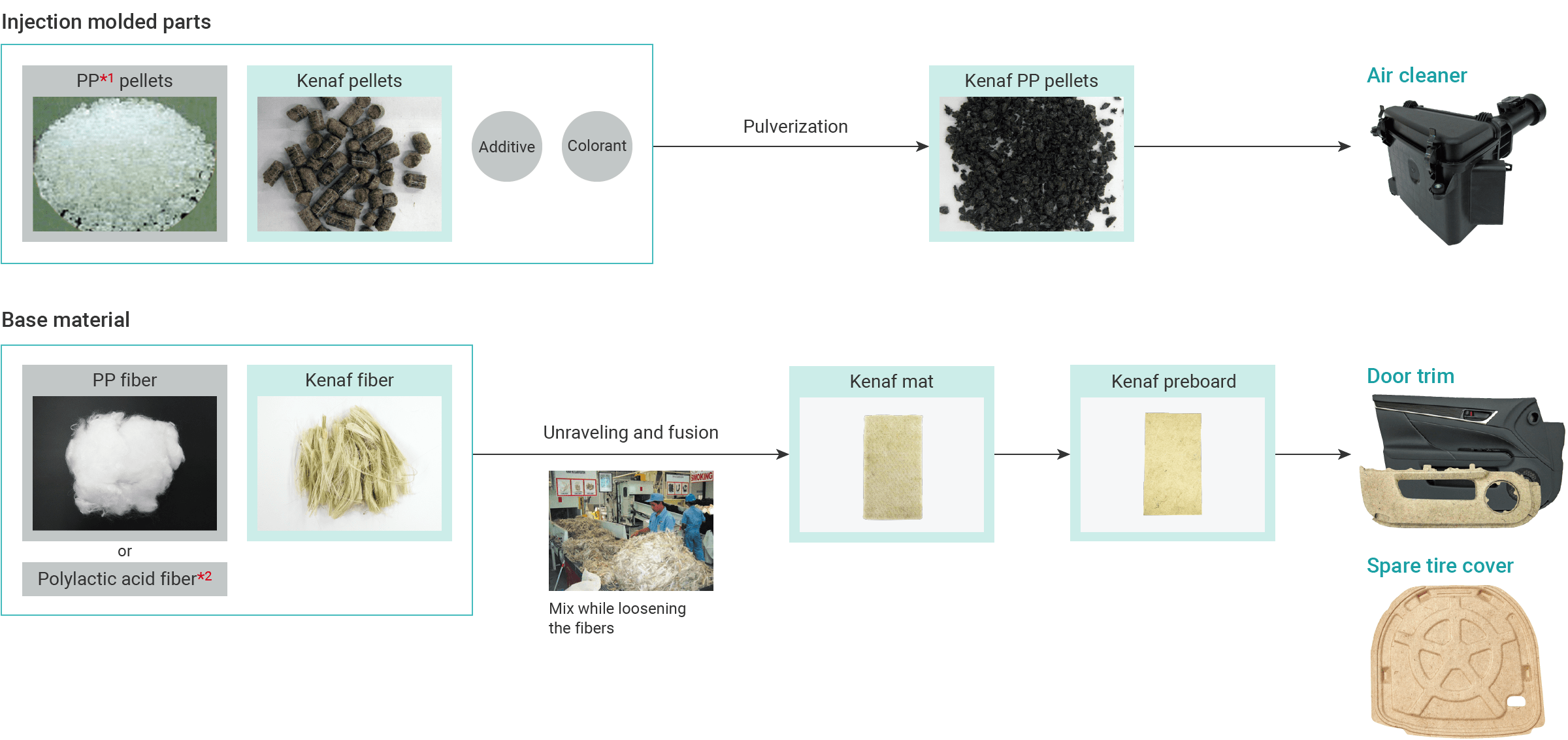
- Abbreviation of the plastic classification: Polypropylene.
- A plant-derived plastic made from lactic acid, which is produced by fermenting starch. It has attracted much interest as a biodegradable plastic material and is also environmentally friendly.
Sequential commercialization of kenaf base materials
Door trim base material using kenaf fiber was first utilized in the Celsior in 2000. Since then, Toyota Boshoku has advanced our technology and expanded usage. Examples include 100% plant-derived parts made from kenaf and polylactic acid, the SBI (Simultaneous Back Injection) method for injection molding of resin parts simultaneously with press molding of kenaf base material, and air cleaner cases made by injection molding using kenaf. Recently, kenaf foam base material, which is one of the world’s top-class lightweight base materials, is employed in the LEXUS LS. Furthermore, we are working to expand the product range by expanding the scope of application; for example, such as utilization in the upper part of the LEXUS UX door trim.
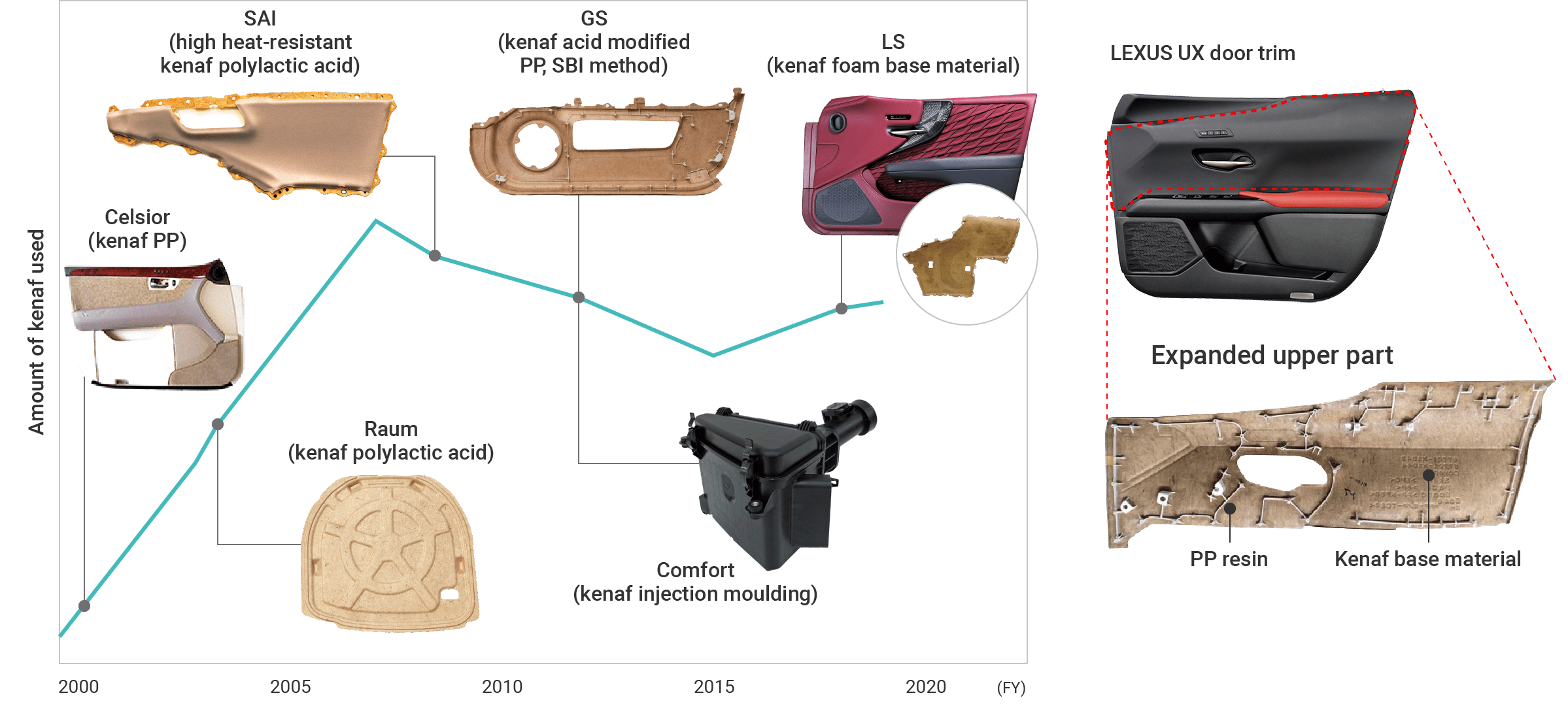
Utilizing kenaf base materials for products other than automobile components
Kenaf processing expertise and technology developed over the years by Toyota Boshoku has been utilized in joint development with Itoki Corporation of a new line of office furniture products made using kenaf base materials. In the future we will continue making use of eco-friendly kenaf base materials to develop new automobile interior products, furniture, and all manner of other similarly more valuable products.
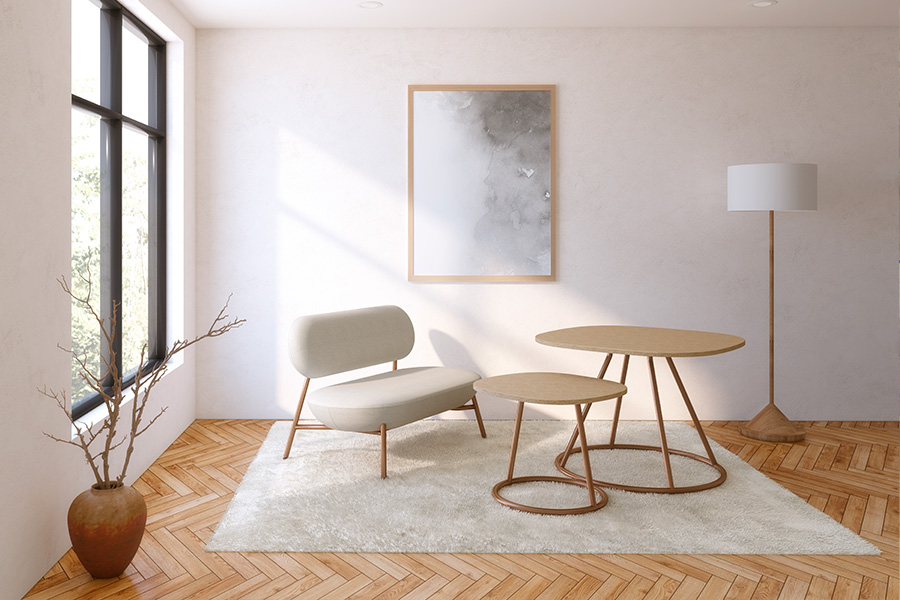
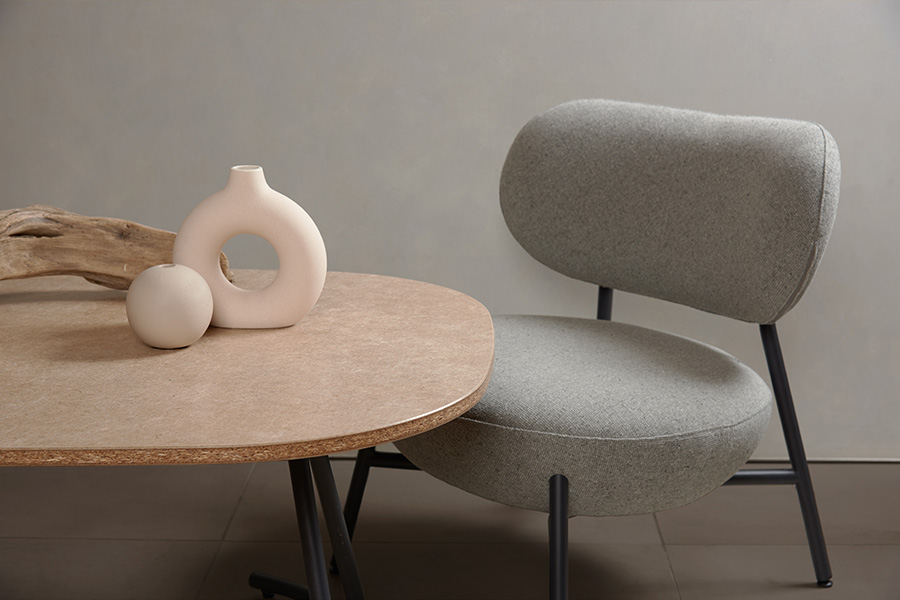