Suppliers
Basic stance
Using fair and equitable procedures, the Toyota Boshoku group purchases raw materials, parts and equipment from a large number of suppliers throughout the world based on our basic purchasing policy. We will grow with our suppliers by putting into practice the spirit of a win-win relationship while fulfilling our social responsibilities in the supply chain with the aim of enhancing corporate value.
Open, Fair and Transparent Trade and Social Responsibility in the Supply Chain
In addition to conducting purchasing activities based on a basic purchasing policy, we are working to fulfil our social responsibility throughout the supply chain.
Basic purchasing policy
- Open and Fair Business
- Mutual Development through Mutual Trust
- Promotion of “Green Purchasing”
- Promotion of Local Purchasing as a Good Corporate Citizen
- Law-abidingness and maintaining Confidentiality
Promoting sustainability activities
Toyota Boshoku and its suppliers adhere to the following items in basic supplier agreements: (1) Respect of human rights; (2) Prohibiting bribery; (3) Ensuring fair transactions; (4) Removing antisocial forces; and (5) Efforts to conserve the environment. Furthermore, we comply with the Antimonopoly Act, subcontracting laws, labor laws, environmental laws, and other related laws in each country and region, and are working to strengthen sustainability activities throughout the entire supply chain.
Every year during Corporate Ethics Month in September, we carry out initiatives aimed towards maintaining and pushing forward with fair and transparent trade. To do this we investigate supplier satisfaction and ask our suppliers to conduct self-assessments in line with our Supplier Sustainability Guidelines, with the overall aim of deepening understanding and spreading the principles of fair and transparent trade throughout our entire supply chain. Additionally, when we start working with new suppliers they are asked to conduct self-assessments.
In fiscal 2024, the allocation of marks and options used in conducting self-assessments were revised to better clarify the issues, and were rolled out at the meeting with suppliers in September 2023. At that time, we reiterated the importance of this being spread and promoted among all their suppliers. Based on the results of the self-assessments, visits to suppliers when necessary, and exchanges of opinions on future points to keep in mind and improvement measures have been ongoing since the previous year.
Self-assessment based on Supplier Sustainability Guidelines
Question items
❶ Compliance
❷ Respect for human rights and maintaining appropriate working conditions
❸ Efforts to conserve the environment
❹ Contribution to society through business activities
❺ Risk management
❻ Developing and deploying guidelines for your suppliers
A survey regarding supplier satisfaction
Question items
❶ Best cost
❷ Requests for rationalization without reasonable grounds
❸ Verification of required quality
❹ Requests for urgent response
❺ Increase in request items due to streamlined operations and reduced overtime
❻ Requests for free-of-charge provision of intellectual property rights and know-how
❼ Demand for money, goods, and services
❽ Purchasing staff’s behavior for suppliers
❾ Disposal of molds used to produce Dies for service parts and the cost of this
❿ Awareness of Declaration of Partnership Building
⓫ Other free opinions (for the entire company including other departments)
Building a global purchasing system
As the Toyota Boshoku group expands our business globally, we will proceed with local purchasing while considering various items such as safety, quality, and cost. At the same time, our entire group will work together with our suppliers to pursue optimal global procurement.
Every year, we hold a Global Annual Supplier Meeting to convey the President’s message and our procurement policy, and to communicate with our suppliers. We also present awards to suppliers who have made significant contributions in terms of R&D, quality, cost, and delivery.
Representatives of commended companies and Sunshine, a supplier group member of Toyota Boshoku, were invited to the 2024 Global Annual Supplier Meeting where we strengthened relationships through face-to-face meetings. In addition, by recording and distributing the contents of the Global Annual Supplier Meeting, we worked to strengthen relationships throughout the supply chain, including our suppliers and their suppliers.
The President’s message, purchasing policy, and other information provided during the Global Annual Supplier Meeting was streamed in Japanese, English, and Chinese.
Training and information sharing
To pursue fair and equitable procurement activities, we hold training sessions not only for members of the Purchasing Division but also for all Toyota Boshoku company members and the Toyota Boshoku group company members in Japan, in an effort to ensure appropriate business transactions.
We also share information on social conditions surrounding the company (compliance, human rights, environment) by holding regular meetings within the Purchasing Segment based on the Supplier Sustainability Guidelines and Toyota Boshoku Group Guiding Principles, and also by storing the materials in a folder that can be viewed globally.
Furthermore, to develop professional purchasing talent, we have established a plan for young department members and DX promotion members to attend external training seminars to promote the improvement of Purchasing Division members' skills. (96% of the planned participation rate in fiscal 2024)
Expansion of global Supplier Parts Tracking Team (SPTT) activities*
The Toyota Boshoku group is promoting global SPTT activities to assure the quality of its products by helping suppliers in other regions enhance their production processes, from beginning with the production preparation stage to getting their businesses on track after the launch of new products. Such actions help create face-to-face ties between suppliers and various divisions, including purchasing, design engineering and quality control, as well as enable problem solving and mutual benefits from different perspectives, notably for such issues as quality, amount, cost, distribution and timely delivery. Additionally, we maintain an SPTT manual for practical global use, and are continuing to standardize our SPTT activities.
We will continue improving SPTT activities and rolling them out globally in order to provide customers with best quality products.
- Supplier Parts Tracking Team activities: Follow-up activities by the team for subcontracted parts production and manufacturing preparation
Toyota Boshoku Group’s Purchasing Information by Each Region
Global
The Americas
Asia
China
Japan
Promotion of green purchasing
Toyota Boshoku recognizes the risks in sustainable development and is committed to the procurement of sustainable raw materials in light of environmental issues such as the effective use of water resources and the creation of a society in harmony with nature. In addition, Toyota Boshoku is strengthening our response to legal compliance related to various environmental regulations in respective countries and regions based on our Green Purchasing Guidelines, and working actively to reduce environmental burden. As part of these efforts, we periodically request certain relevant information from our suppliers, such as CO2 emission levels and the results of tests done to confirm that substances with harmful environmental effects are not being used. We also require our suppliers to establish environmental management systems (EMS) based on the acquisition of ISO certification aimed at creating a sustainable society.
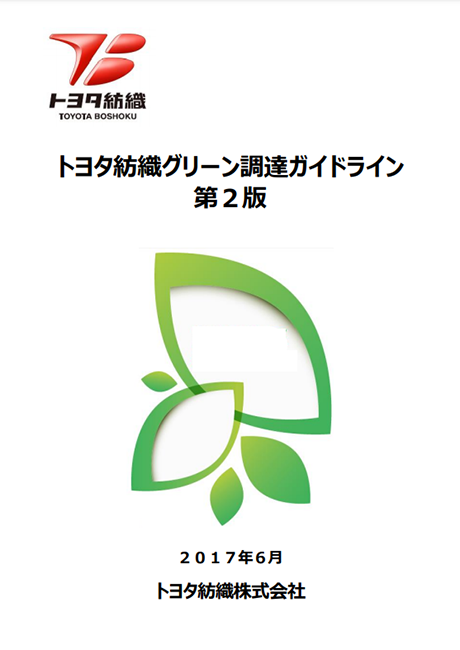
Studying with our suppliers
Initiatives taken together with our suppliers
We are committed to mutual learning activities to enhance the competitiveness of our major suppliers.
In response to suppliers’ needs, and with an aim toward strengthening functionality, a supplier’s personnel may be seconded to work within the Toyota Boshoku Group. In addition, we support the activities of Sunshine—a supplier group member of Toyota Boshoku with the aim of enabling mutual study and the sharing of exemplary examples between organizations. More specifically, we hold study groups on safety, health, and improving product quality, and we promote both the sharing of good, learnable examples and the resolution of problems faced by suppliers.
Finally, we run a study meeting concerning carbon neutrality and other social issues.
Held a management seminar run by Sunshine
At a management seminar run by Sunshine (a supplier group member of Toyota Boshoku), officers of Toyota Boshoku and representatives of Sunshine discussed issues and measures such as securing human resources and cost effectiveness under the theme of "DX support in MONOZUKURI competitiveness" to educate suppliers on how to secure MONOZUKURI competitiveness.
Hosting of Decarbonization School by Sunshine
We are committed to supporting our suppliers' carbon neutrality initiatives and have held the "Sunshine Decarbonization School," which is organized by Sunshine, a supplier group member of Toyota Boshoku, since fiscal 2023. Outside consultants and representatives from the Carbon Neutral Environmental Center act as lecturers at the School, teaching energy-saving techniques and how to develop CO2 reduction plans. In addition to assisting member companies in setting goals and creating plans, this also supports the development of human resources who can work toward carbon neutrality over the long term.
We will continue to work closely with our suppliers to promote carbon neutral initiatives that are integrated with the supply chain.
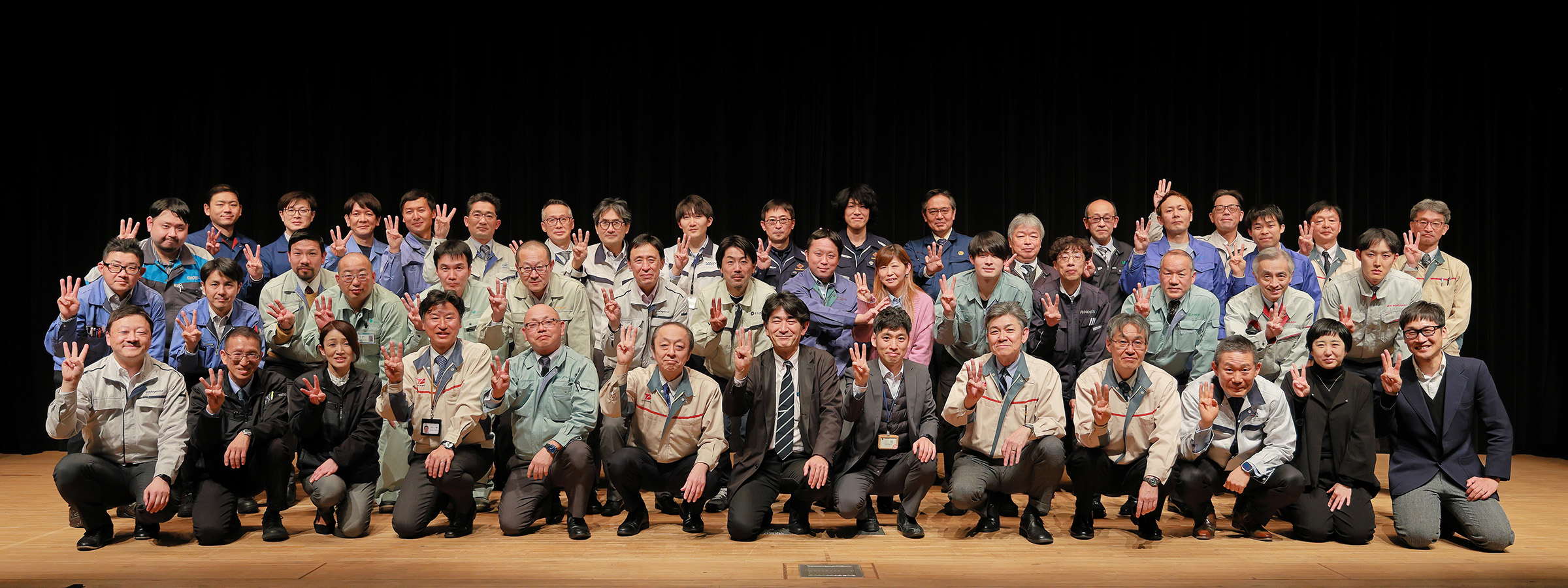