生産性向上をもたらす制御盤の小型化
省スペース化で挑む生産性向上
「生産性向上」と聞くと、多くの方が生産工程上のムダを排除し、短い時間で効率的に生産することを想像するのではないでしょうか。しかし一般的に製品1つ当たりで短縮できる時間は秒単位。生産量を増加させるのは、簡単ではありません。
生産量を格段に増やすためには、どうしたらよいのか。工場の面積を変えずに、限られたスペースの中で生産ラインを増やすことがその一歩になると考え、生産ライン自体の見直しや設備を小さくするといった、「生産に必要なスペースを小さくすること」に取り組み始めました。省スペース化を実現するために挑んだのは、溶接設備に付随する制御盤の小型化でした。
制御盤の小型化に挑戦
制御盤の小型化に向け、まず「制御盤単独での専有面積ゼロ」を目標に掲げました。
「専有面積ゼロ」とは、ロボットを制御するロボット盤の上部部分にある空いた空間を活用し、制御盤で専有する面積をゼロにすることです。また、対象を小型化の実績があった非ロボット設備ではなく、より難易度が高いロボット設備※とし、国内の全溶接設備に対応できるようにしたいと考えました。
- ※ 要求される安全性能の値が高く、故障時の自己判断機能が必須。そのため、複数の配線や安全機器の取り付けが生じる
ロボット盤の上に制御盤を載せるための課題
- 制御盤のサイズを従来の半分にする必要がある
- ロボット設備は装置が多く複雑だが、制御盤のサイズを小さくするためには、部品自体を小型化しなければならない
取り組み 1
① 部品の小型化
制御盤内でスペースをとる配線格納用のダクトを廃止。配線を短くすることができるプッシュイン機器を活用
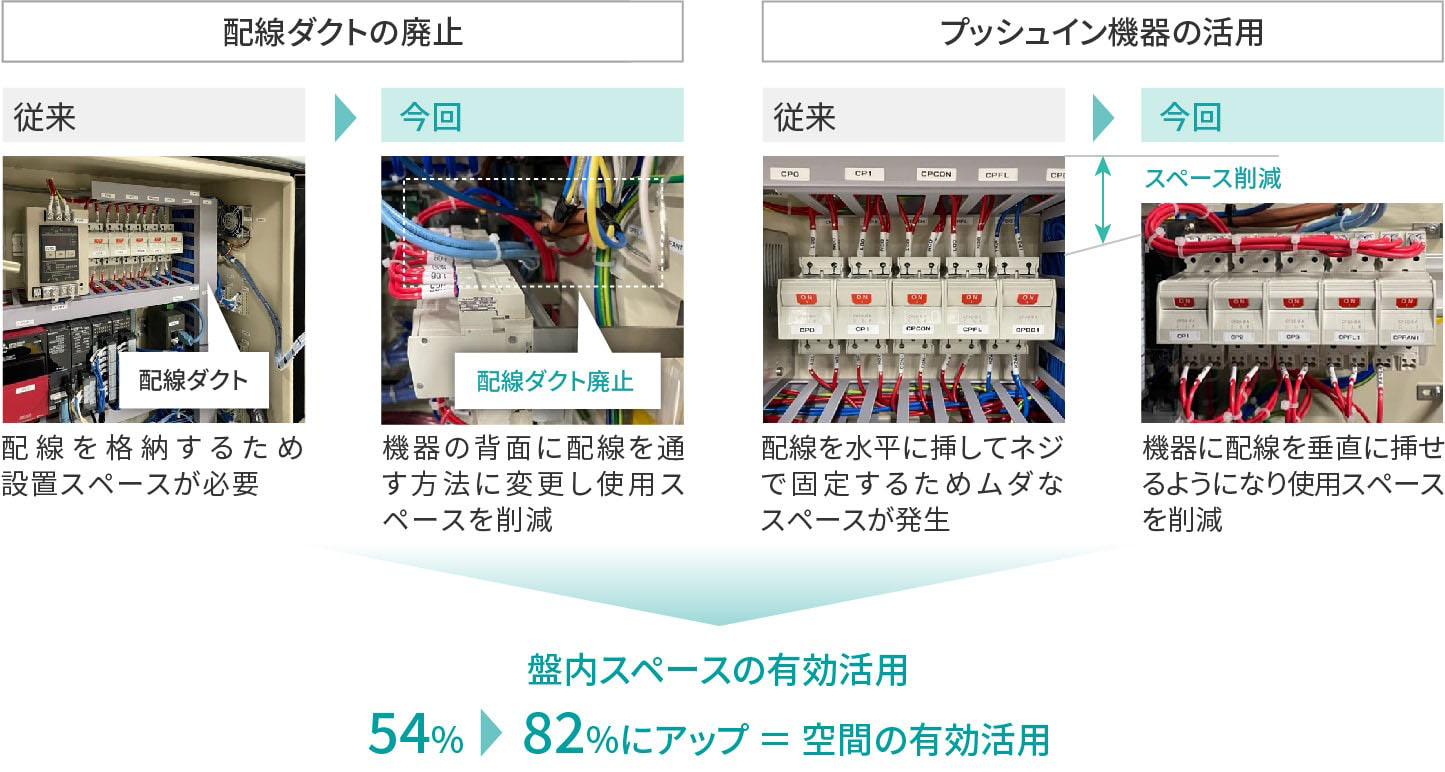
② 温度対応
小型化によって制御盤内の温度が上がり過ぎないように、従来より大きいファンを設置し一定温度をキープ
③ 制御盤内の機器配置
従来の制御盤内の機器配置を見直し、内部を三次元的に活用することにより必要な機器をコンパクトに配置。側面に機器を配置するとメンテナンス作業に不便が生じることから、側面2面と背面を扉タイプに変更することで、保全性を維持
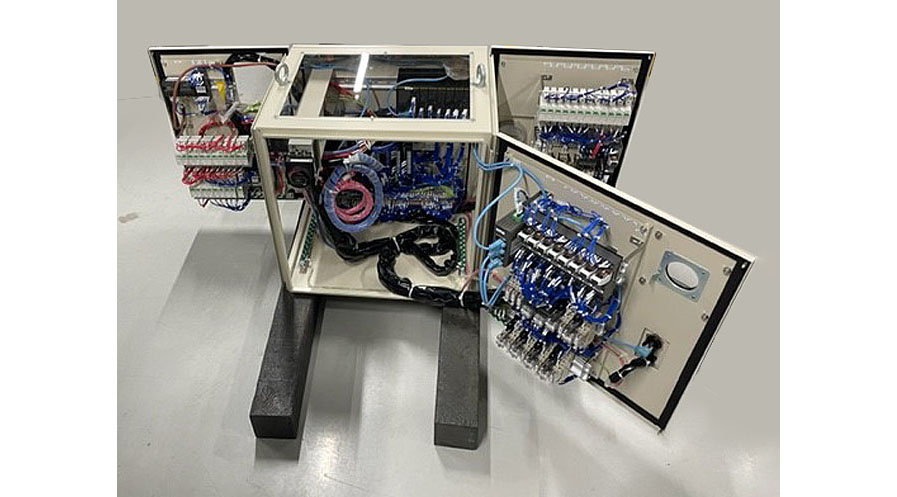
しかし、ここで新たな課題が生じました。制御盤が小型化した一方で、機器や配線数は変わらないため、制御盤内が複雑になってしまい、メンテナンス作業が煩雑化するという声が現場の作業者から上がったのです。
そこで、当社が車内のイルミネーション製造で得た基板に関する技術やノウハウを生かし、省配線化、部品小型化のために、機器を基板化することにしました。
取り組み 2
- 置き換え可能な機器を選定して、基板化を実施。配線の数を大幅に減らす
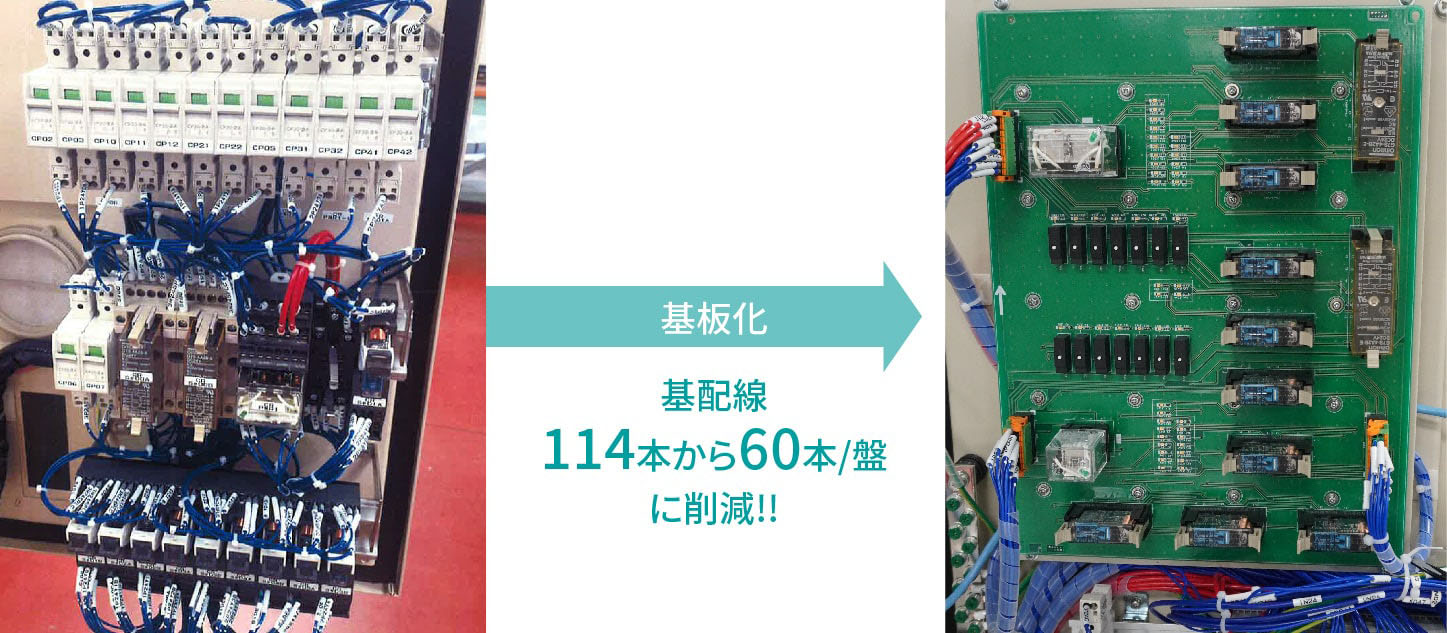
基板化すると配線がなくなるため、故障した際に、今までのように保全担当者が配線を一つひとつ確認するというやり方が通用しなくなりました。そのため、基板上の各機器に対応したLEDを設置し、点灯/消灯状態で故障個所が見てすぐにわかる工夫をしました。そして、担当者向けに、新基板に関する説明会を実施しました。
基板上の各機器に対応したLEDを設置
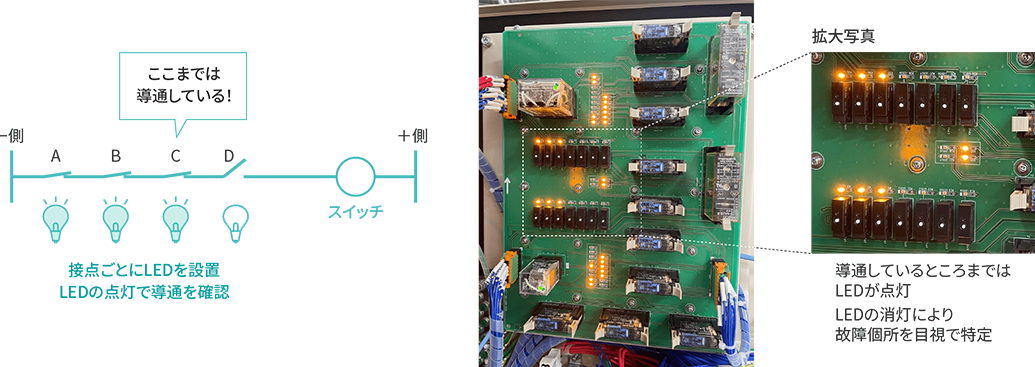
これらの取り組みをふまえて、今後、実際の生産ラインに小型化した制御盤を設置していきます。日本以外の国では法規制などが異なるため、単純に横展開することはできませんが、さらなる改善を行い、日本以外での導入も目指します。
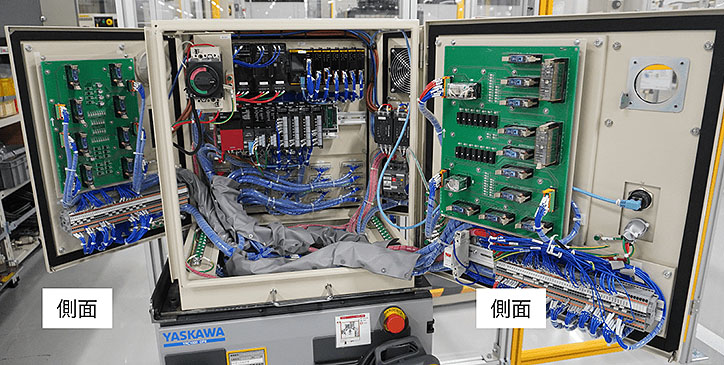
効率的に、高品質な製品を届ける
制御盤の小型化に取り組んだことで、設備スペースの縮小、そして、故障時の工数削減を実現しました。
さらに、配線を用いた機器に比べて、配線のない機器は故障率が減ると考えられています。故障しない設備をつくる。それこそ正に、革新的。実際の生産ラインへの導入後、効果検証を行っていきます。
トヨタ紡織はお客さまへ品質の高い製品を届けるために、さまざまなアプローチを通し、ものづくりにさらなる革新をもたらしていきます。
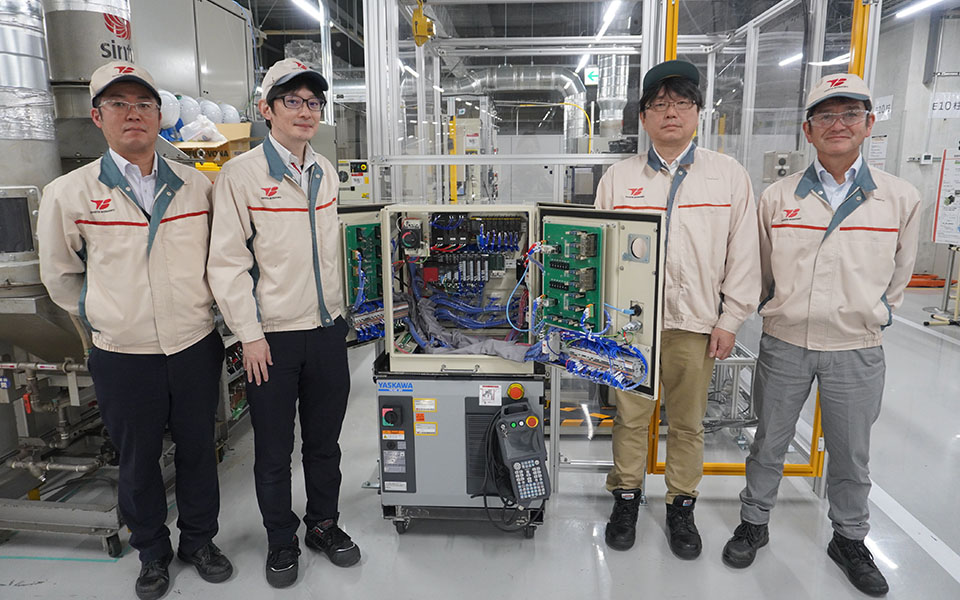