Downsizing of control panel brings improved productivity
Tackling space reduction to improve productivity
When most people hear the term “productivity improvement,” they probably think of eliminating waste in production processes and producing more efficiently in less time. Generally, however, the time that can be saved per product can only be counted in seconds. Increasing production volumes is not easy.
So what can be done to increase production more dramatically? Thinking that increasing the number of production lines in the limited space available without altering the factory floor area would be a step in this direction, we began working on reducing the space needed for production by reviewing the production lines themselves and making the equipment smaller. The challenge to save space was to downsize the control panel accompanying welding equipment.
Challenge to downsize the control panel
To downsize the control panel, we first set ourselves the goal of having zero area dedicated to the control panel alone.
This meant making use of the open space in the upper part of the robot panel that controls the robot, thereby reducing the area occupied by the control panel to zero. Also, rather than the non-robotic equipment, which had already been downsized, we wanted to target the more problematic robotic equipment,* so that measures could be applied to all of our welding equipment in Japan.
- * Robotic equipment has a high safety performance value requirement, and self-diagnostic functionality is essential in case of a failure. This results in the installation of multiple wires and safety devices.
Challenges in placing the control panel on top of the robot panel
- There was a need to reduce the control panel to half of its previous size.
- Robotic equipment is complex, with multiple devices, and so the components themselves must be downsized if the control panel is to be made smaller.
Initiative 1
(1) Downsizing of components
Remove ducts for wiring that take up space in the control panel. Utilize push-in devices that can shorten wiring.
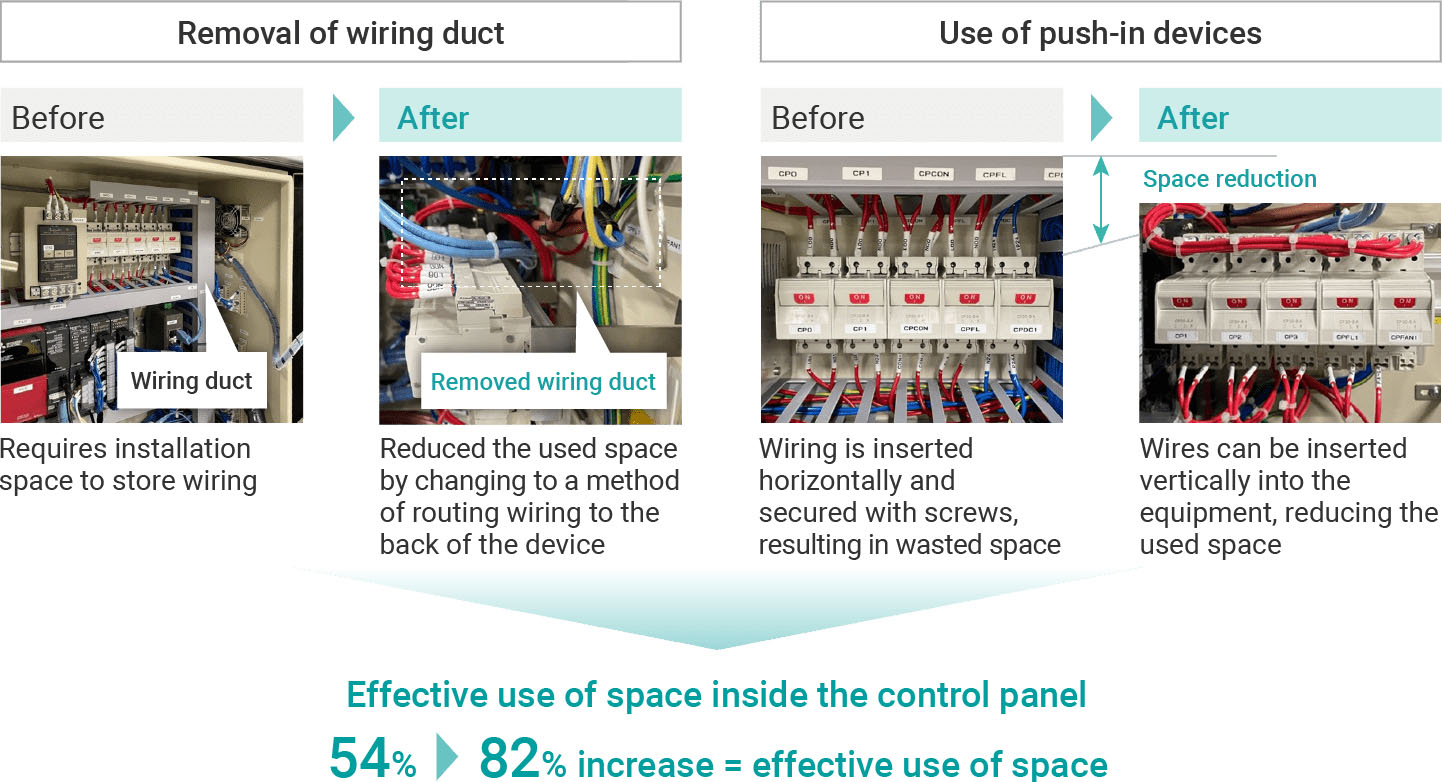
(2) Addressing temperature
To prevent the temperature inside the control panel from rising too high due to the downsizing, a larger fan was installed to maintain a constant temperature.
(3) Layout of equipment in the control panel
We reviewed the previous layout of equipment in the control panel and arranged the necessary devices in a compact manner by utilizing the inside of the panel in three dimensions. Since placing equipment on the sides makes maintenance work inconvenient, the two sides and the back were altered to a door type structure to preserve maintainability.
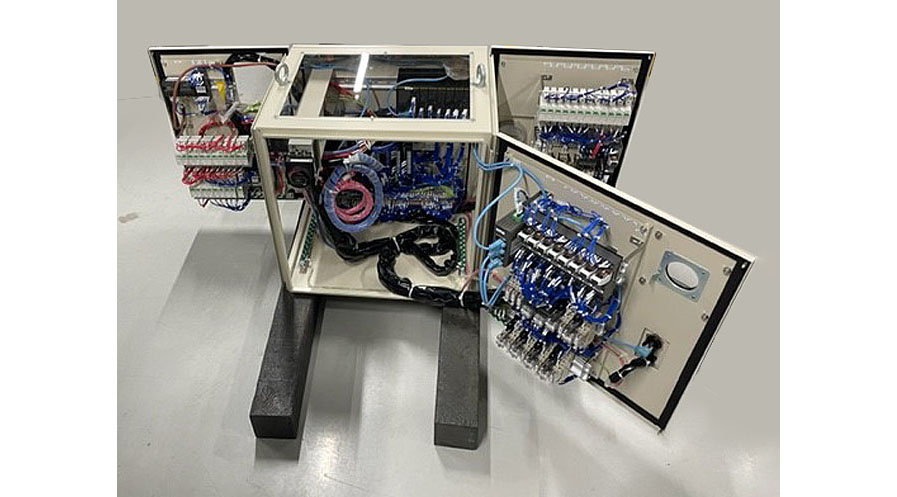
However, a new challenge arose here. While the control panel was smaller, the number of devices and wires remained the same, making the inside of the control panel more complex. As a result, on-site workers voiced their concerns that maintenance work had become more complicated.
Therefore, we decided to convert the equipment to an assembly board to reduce wiring and downsize the components, taking advantage of our assembly board-related technology and expertise acquired through the manufacture of in-vehicle illumination.
Initiative 2
- Select replaceable devices and implement board conversion. Significantly reduce the number of wires.
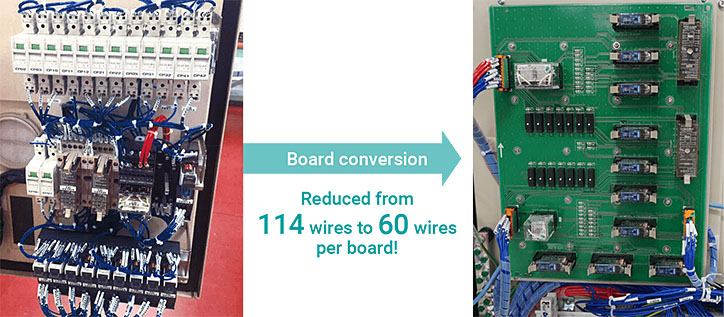
As conversion to an assembly board eliminated wires, the conventional method of having maintenance personnel check the wiring one by one in the event of a failure no longer worked. To address this issue, LEDs corresponding to each device on the board were installed so that the fault location could be identified based on whether the LED was lit or unlit, and a briefing session on the new board was held for the responsible personnel.
Installation of LEDs corresponding to each device on the assembly board
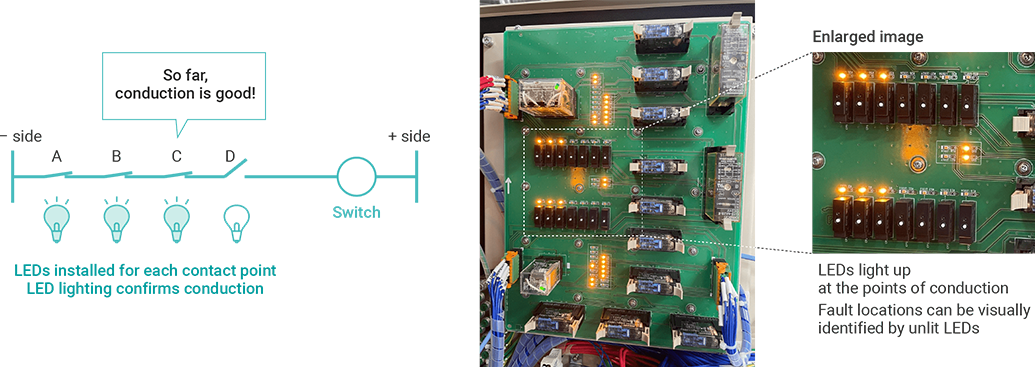
Based on these initiatives, we will install downsized control panels on live production lines going forward. Although we cannot simply roll out the system horizontally due to the differing laws and regulations in other countries, we aim to make further improvements and introduce it outside of Japan.
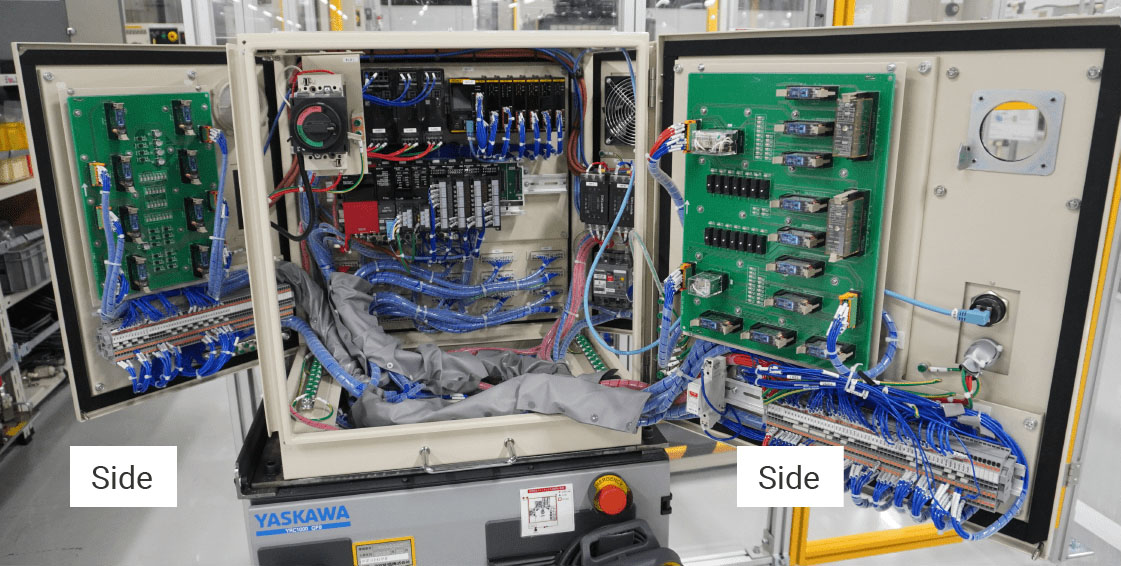
Delivering high quality products, efficiently
Our efforts to downsize the control panel have resulted in a reduction of equipment space and also of the man-hours required in the event of faults.
What’s more, wire-free equipment is likely to have a reduced failure rate compared to wired equipment. Creating failure-free equipment: now that is innovative! Following its introduction on live production lines, we will verify the effectiveness of the equipment.
To deliver quality products to our customers, Toyota Boshoku will bring further innovations to manufacturing through a variety of approaches.
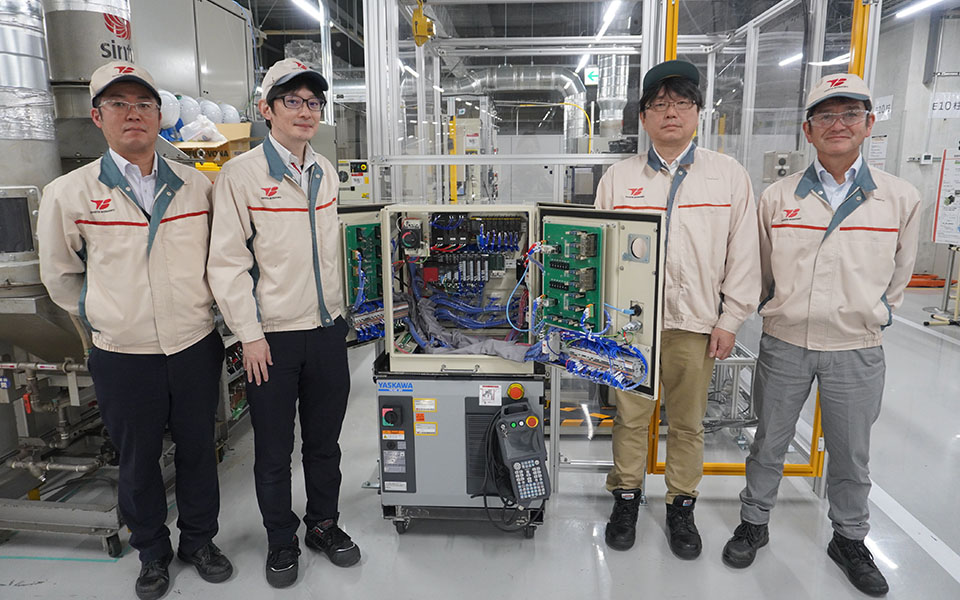