Aiming for a workplace that is bright and enjoyable for all
Original sign language to facilitate communication with hearing-impaired company members
The sewing process at the Sanage Plant welcomed two hearing-impaired company members in 2017. At that time, during morning and lunch meetings the group leader would verbally deliver a message to be communicated, which was then written down and passed on to the company members by the team leader. However, some group leaders and team leaders were concerned about whether the content was being conveyed correctly, and company members were also worried about the time it was taking to exchange information, even if they did not fully understand what was being conveyed, making it difficult to confirm the details. To solve this issue, morning meetings are now conducted using a large monitor, which increases the amount of visually available information and improves the accuracy of information transfer.
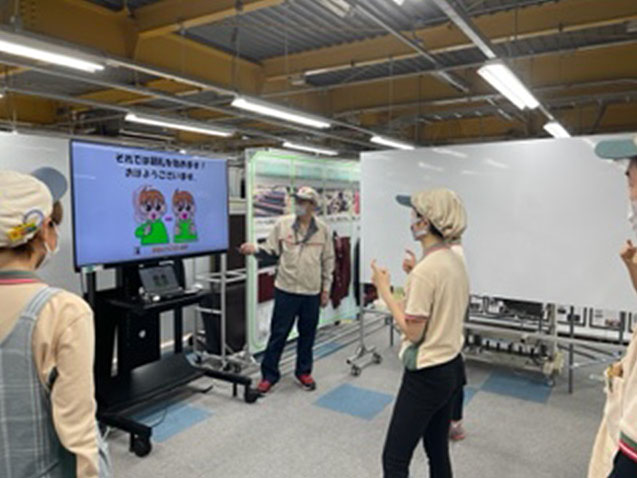
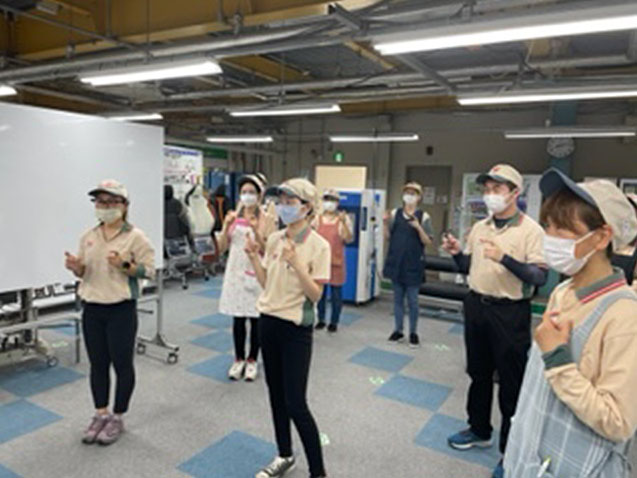
In the sewing process, work must be stopped the moment a defect is found, a member in charge of correction is informed about the defect, and he or she then fix this. The challenge is how to communicate defects quickly and accurately so that production does not stop for long periods of time. Before adopting the original sign language, they had been communicating problems to each other in writing, but this was time-consuming and it was difficult to tell whether each other's intentions were being accurately conveyed.
Members in the workplace have always wanted to communicate with their hearing-impaired colleagues as well, so they learned simple sign language such as "good morning" and "thank you." Inspired by this, an original sign language was created for sewing defect jargon such as "wrinkle" and "tucked seam." It was finalized following a series of discussions about how they could best communicate quickly and accurately, from each member's individual perspective.
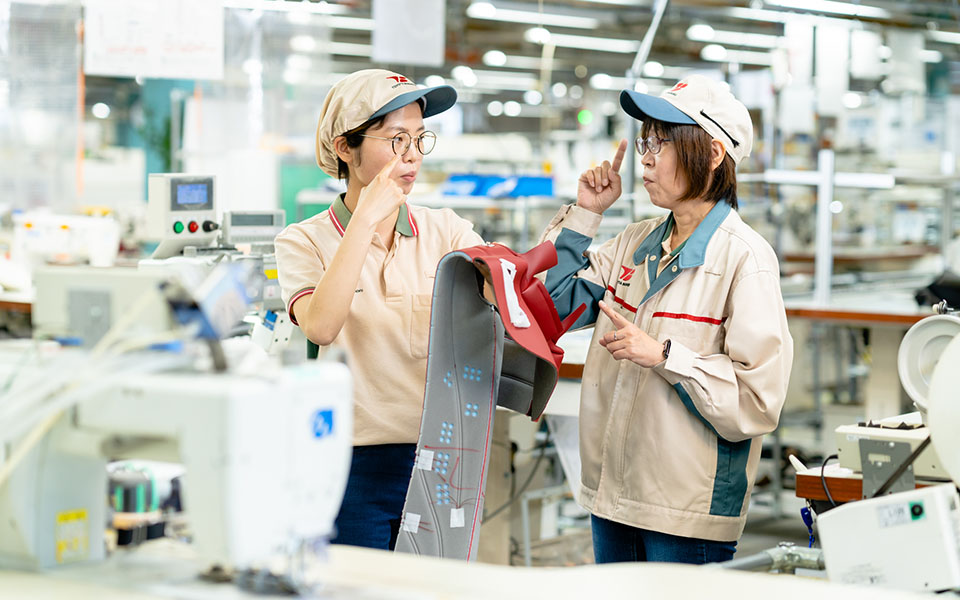
Seeing existing company members working so enthusiastically gave students confidence to join the company
The sewing process at the Sanage Plant now allows for easy and smooth communication through the original sign language. Furthermore, this "common language" eliminates the anxiety of not knowing whether the message is really being conveyed. This boost to communication during work has also had the beneficial side effect of encouraging even closer communication during breaks when written communication or smartphones can be used.
These efforts have spread to a nearby school for the deaf that runs clothing courses, leading to an increase in the number of students coming to the company for practical training. After three weeks of practical training, the individual can join the company a year later if they wish. As of July 2022, all the students who have experienced practical training have joined Toyota Boshoku.
Making sure to avoid trouble in daily life
For example, in the event of an earthquake or other disaster, an emergency broadcast may be played in the plant. If evacuation is immediately required, the people around you will naturally call out to you. However, if this isn't possible or if the sound of an emergency broadcast alone is not enough, hearing-impaired company members will not immediately know what has happened. To resolve this problem, lights were installed at the entrances to workplaces, near restrooms, and on fire doors, which light up in an emergency. If the light is illuminated, you know that you are in an emergency situation and must take some action. Even in fire drills, the entire workplace is trained to be aware of hearing-impaired company members and act accordingly.
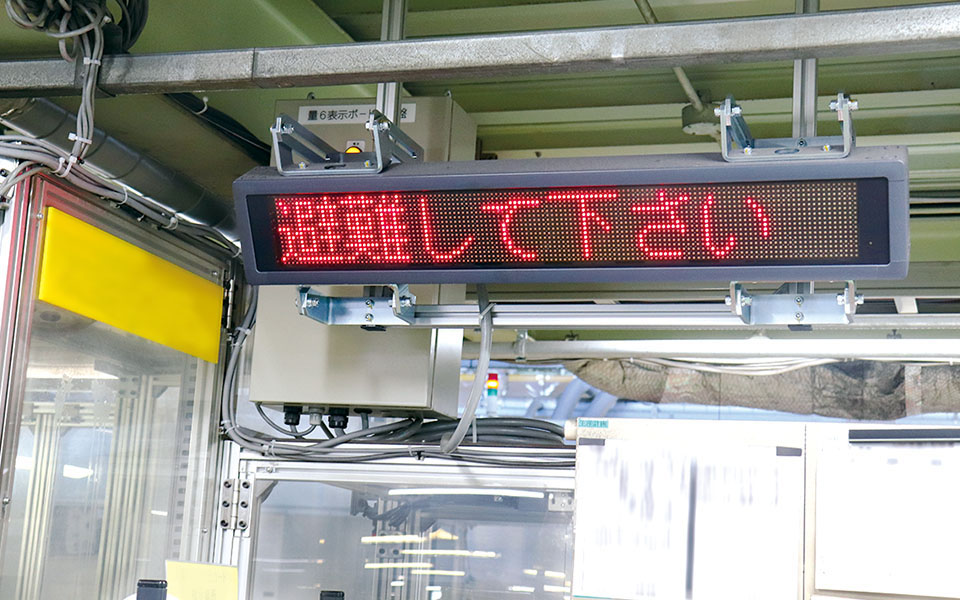
Greater ease of working for members who work shorter hours
There is also the Nanohana (canola flower) Process at the Toyohashi Plant, which has been devised to create a workplace that is more comfortable for members who work shorter hours. The Nanohana Process produces door trims for a small number of car models. Unlike other general production lines within the company, this process allows a certain amount of inventory to be retained, and for the assembly of components to be completed by one person, making it possible to accommodate sudden absences due to the illness of a child or other reasons. On a normal line, if you take a day off or leave early, your coworkers have to take your place, so some company members were hesitant to do this because they were concerned about how this would affect those around them. However, in the Nanohana Process, they do not need to be unnecessarily concerned as everyone feels that they are "in the same boat." The process also allows members to view the annual schedule of events at daycare centers and elementary schools attended by members' children, as well as a flowchart in the event of urgent communications from such centers or schools. The process ensures that all company members are aware of each other's situation, rather than feeling unable to share issues.
We will continue to embrace diversity and make various innovations to create a workplace where everyone can work comfortably.
